Funding: Spanish Ministry of Economy, Industry and Competitiveness (MINECO) (National R&D Programme for Societal Challenges) (DPI2015-67667-C3-1-R)
Partners: Mondragón University, Technical University of Madrid and IMDEA Materials Institute (coordinator)
Region: Spain
Project period: 2016 – 2018
Principal Investigator: Prof. Ignacio Romero (ignacio.romero@imdea.org)
Machining of metals is a crucial manufacturing process whose market is estimated to be of the order of 5% of GDP in developed countries. Despite its relevance, the physics of the problem are not well understood and the precise selection of operation parameters has to be tuned by trial and error in many cases (e.g., to ensure the proper tool life or surface integrity conditions in machined components). The next generation of airplane engines, those that can provide increased thrust with reduced environmental impact, require improved machining technologies that can only come from significant advances in the understanding of this process.
In this project, we propose a multidisciplinary approach to enhance the comprehension of metal machining. For that, we identify three topics that need to be analyzed in order to improve this technology: 1) the development of accurate material models that incorporate the mechanisms of plasticity at the crystal level, as well as the effect of temperature over them; 2) the implementation of robust numerical methods that can upscale the former material models to the macro scale, and remain accurate despite the large deformations in the workpiece; 3) the validation of all material and numerical models with reliable experimental data coming from machining benchmarks, including temperature and microstructure measurements. Related with these three aspects, the research groups collaborating in the project combine complementary expertise in material science, numerical modeling, and machining, as well as access to the necessary experimental and computational facilities.
Exploiting their current know-how, and taking advantage of the benefits of multidisciplinary collaboration, the project objective is to develop material and numerical methods that can be employed for the predictive simulation of machining processes. The material models will extend current crystal plasticity formulations to include the temperature and strain rate effects on the visco-plastic behavior, including the behavior under very large strain rates and a full thermo-mechanical coupling including conduction of heat and heat generation by plastic work; the numerical models will exploit thermodynamically consistent integrators to obtain robust constitutive discretizations and meshless methods to sidestep the difficulties derived from mesh distortion; finally, the models derived will be validated with real data (forces, temperature, strain or stress rates) obtained from machining processes in different cutting conditions.
The expected outcomes of the project are of two types: on the one hand, fundamental contributions to material modeling and simulation of thermomechanical processes under severe conditions; on the other, technological improvements in simulation tools and predictive capabilities in machining processes. Given the interest of ITP in incorporating the results of this project in their manufacturing processes for cleaner airplane engine components, the project will be aligned with the strategic program of R+D+I of the Spanish government and the European H2020 framework.
Partners
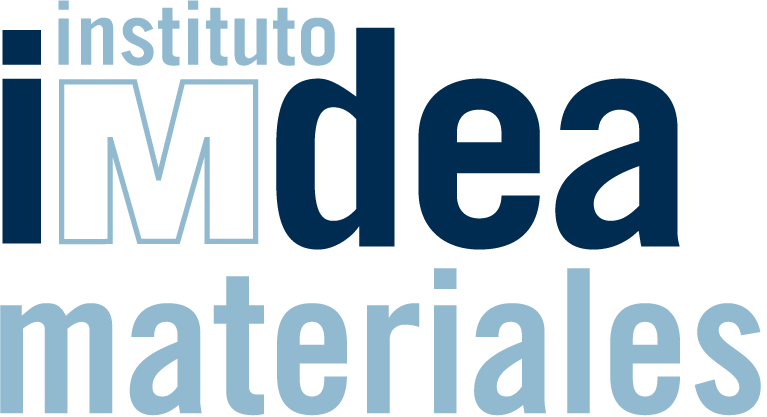
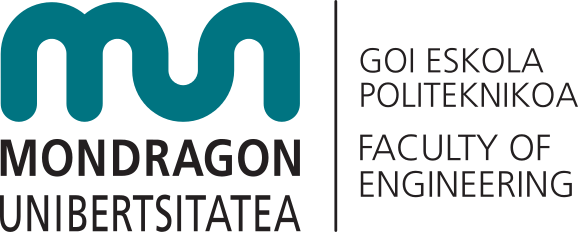
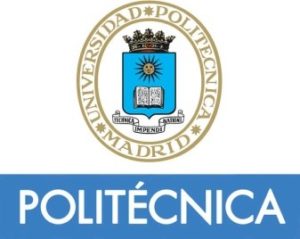
Funded by
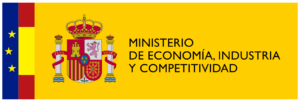