Design and Optimization
With the main aim of weight reduction that heavily impacts fuel related emissions in the transportation industry, the group develops non-conventional composite designs that take full advantage of the orthotropic nature of composite materials and of current automated composites manufacturing capabilities. Examples are dispersed-ply laminates and steered-fibre composites. Employing evolutionary optimization strategies and reliable representation of the composites behaviour, such configurations are designed for optimal stiffness, buckling, failure and damage tolerance responses. A numerical tool (Viper) has been developed to predict the mechanical properties of fibre-reinforced composite laminates
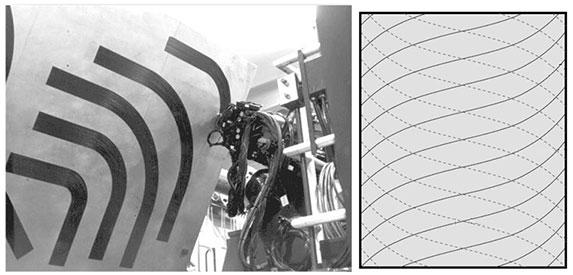
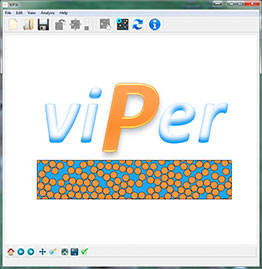
Multiscale Numerical Simulation
The group is developing a Multiscale Virtual Design and Testing approach that allows the numerical simulation of composites at Ply, Laminate and Structural scales from the measured properties of their constituents (fibres, matrix and fibre/matrix interfaces). The material behaviour at the lower scales is homogenized into physically-based constitutive models that conveniently model the response at the higher scales. This approach is used for the virtual testing of composites and in the design of novel composites configurations at different scales.
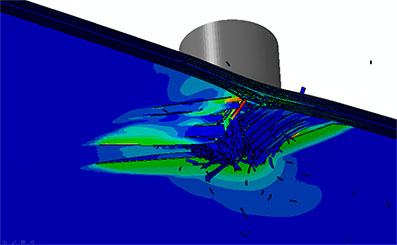
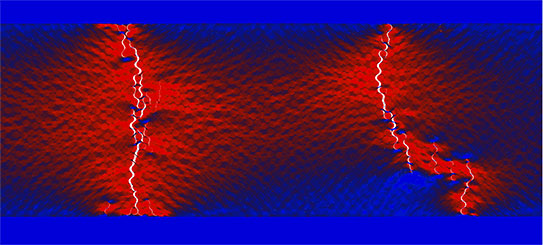
Process Simulation & Manufacturing
The group is also involved in several projects related with manufacturing of advanced structural composites, fibre reinforced thermosets and thermoplastics, by means of autoclave consolidation of prepregs as well as out-of-autoclave techniques such as resin transfer moulding RTM, resin infusion, VARI, pultrusion, hot forming, out-of-autoclave prepregs, etc. In parallel, the research is highly focused on the development of advanced multi-physics numerical tools to investigate the influence of the processing variables on the final quality and mechanical performance of the composite material.
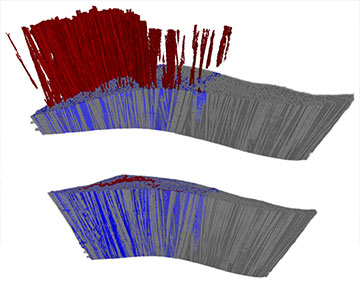
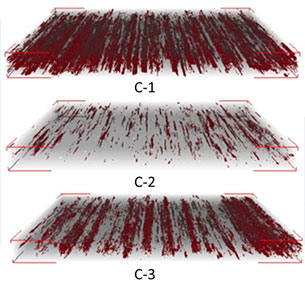
Mechanical Testing
The group has also acquired a solid experience in the field of mechanical characterization of structural composites under different loading conditions and lengths scales. Independent characterization methods at the microscale were developed in collaboration with the Nanomechanics group at IMDEA Materials to determine the matrix, fiber and fiber/matrix interface strength in composite materials to be used in micromechanical models. The determination of the macroscopic stress-strain curves as well as the assessment of the damage mechanisms and their evolution during loading at the coupon level allowed to validate high fidelity multiscale models.
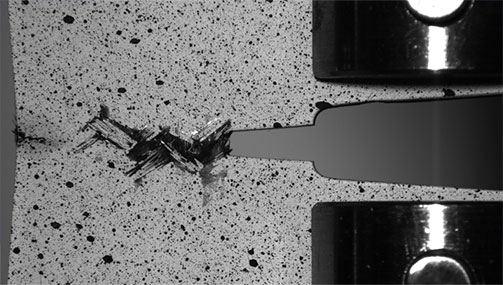
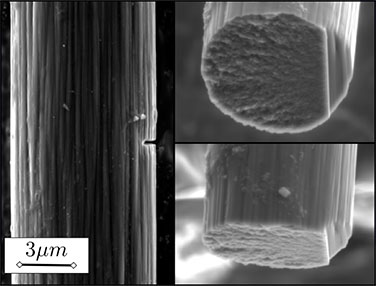