Funding: Ministerio de Ciencia e Innovación. Proyectos de Colaboración Internacional – 2021
Region: Spain
Project period: 2022 – 2024
Supervisor: Dr. Damien Tourret (damien.tourret@imdea.org); Fellow: Rouhollah Tavakoli (rouhollah.tavakoli@imdea.org)
Metal Additive Manufacturing (AM) has an enormous disruptive potential in aerospace, marine, automotive, healthcare and energy sectors. Yet, in spite of decades of research and development, major scientific, technological, and economic challenges remain. For instance, only a few commercial alloys can be reliably printed. A key obstacle relates to expensive and time-consuming trial-and-error experiments required during the typical process/product design cycles. Considering that physical and mechanical properties (measures of quality) are function of microstructure, the prediction of the latter by means of computer simulation stands out as a most promising pathway to reduce the number of experiments and thus accelerate innovation. However, metal AM is a deeply multiphysics process, including a wide range of time and length scales, making its computer simulation challenging theoretically as much as computationally.
This project entitled Micro/Macro-Modeling of Solidification in Additive Manufacturing (MiMMoSA) is grounded in the hypothesis that models for macroscale processing and microscale microstructure formation are now predictive enough that, combined with high-performance computing and novel multi-scale coupling methods, it is possible to predict the microstructure of additively manufactured metallic alloys components directly from computational simulations.
The project aims at developing an efficient computational tool to accurately predict the microstructure of parts additively manufactured by Selective Laser Melting (SLM) process under industry-relevant conditions. To do so, a multiscale computational framework will be developed, combining microscale and macroscale solvers coupled through an original multiscale bridging technique. Properties of complex alloys will be computed by thermodynamics calculations. Advanced acceleration techniques (e.g. multi-GPU-multi-CPU parallelization; use of alternative function spaces; advanced stable time
stepping schemes) will be put in place in both macro- and micro-scale simulations in order to address length and time scale limitation. Finally, a validation of results is to be performed using available benchmarks in the literature, experimental data from various projects at the host organization, as well as selected independent experiments to be performed using the SLM and characterization equipment at the host. In addition to generating new scientific knowledge, the completion of the project will result in an open-source professional and reusable software tool to predict thermal history and microstructure in industry-relevant SLM AM scenarios. As such, it will promote and accelerate the implementation of digital twins for AM in industry. To increase its impact, we will target a range of metallic alloys of high industrial impact, such as Ti-based (e.g. Ti- 6Al-4V), Nibased (e.g. Inconel 718) and Mg-based (e.g. Mg-Ca-Zn or Mg-Y-RE-Zr) alloys as targeted systems.
The impact and reach of the action will be further increased by a variety of dissemination and communication actions, such as scientific publications in high-impact scientific journals, and a broad range of activities aiming at a broad non-specialist audience in the form of publications in non-technical outlets, outreach events for young and non-technical audiences.
“This project (PCI2021-122023-2B) is funded by MCIN/AEI/10.13039/501100011033 and by the European Union “NextGenerationEU”/PRTR.”
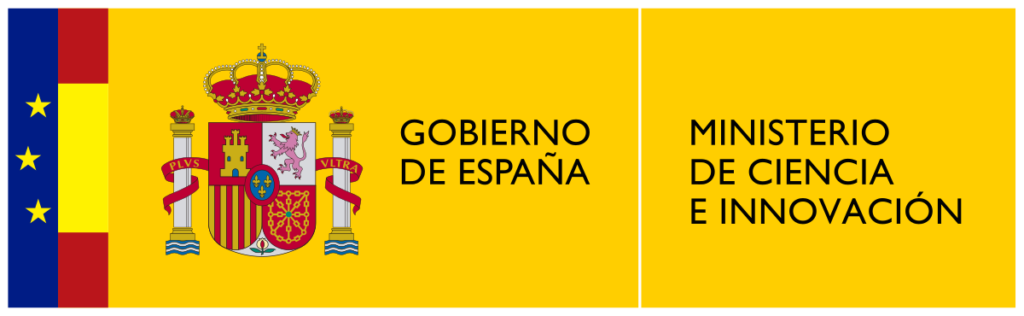
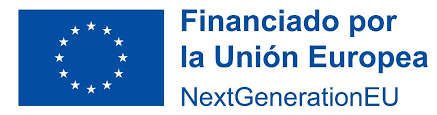
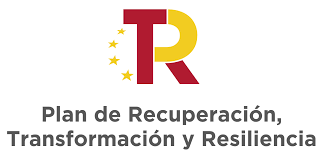
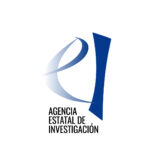