Project details
Funding: Public-Private Partnership 2022.
Project coordinator: HP Printing and Computing Solutions S.L.U.
Project period: 01/12/2023 – 30/11/2026
IMDEA Materials' researchers
Dr. José Manuel Torralba
Dr. Federico Sket
Abstract
Today’s society demands clean manufacturing processes that consume low levels of energy and respectful with the consumption of raw materials, while being capable of mass-producing of high-performance components in order to meet the request of industries as demanding as that of the automotive. The project presented here meets all the above premises. Starting with an additive manufacturing technology based on binders and sintering (Metal Jet Technology), developed in Spain, an in-depth review of the technology is proposed to make it robust and ready to enter the high-performance components manufacturing market. The complete vision of the process (printing, removal of the binder and sintering), presents a sustainable and efficient “near net-shape” technology. Through a complete study of the recyclability process of used powders, of the printing variables, the parameters linked to the elimination of the binder and sintering, it is proposed to prepare a process guide
that allows the jump of the technology to the market. The project contemplates, as a preliminary step, the development of a proof of concept of the technology. The project also has two companies that can cover the entire manufacturing cycle: on the one hand, HP, which has the experience and capacity to produce components by 3D printing (being able to be considered a benchmark in the development of printing methods), and AMES, a key player in the Spanish powder metallurgical sector, with extensive experience in the development of stainless-steel components for the automotive industry. As a complement to both companies, the IMDEA Materials institute has a high capacity to develop materials and their characterization.
From a technological point of view, the project starts with a complete study of the raw materials to be used (powder and binder) with the idea of generating the appropriate metrics that allow both reusability and the layout of the inks used in the composition of the binder. The idea of being able to convert reused powder into new powder is linked to the optimization of raw materials and an improvement in the circular economy. The
next important milestone is the definition/optimization of printing parameters. Once the materials have been printed and before undergoing the sintering process, the removal of the binder necessary for printing must be optimized. These two stages could be done subsequently in the same thermal cycle, which would facilitate and optimize the manufacturing process.
At all stages of the project, a lot of data will be generated, and in a project where data generation is important, having the ability to analyze it properly and extract relevant information becomes a fundamental task. As a whole, it can be considered a highly multidisciplinary project with complementary disciplines (such as material science -an important approach is made from the basis of MSE-, metallurgical engineering -dealing with the physical metallurgy of the stainless steels-, organic chemistry -which is needed to the development and elimination of binders-, manufacturing -3D printing, sintering-, and artificial intelligence to accelerate data processing and extraction of relationships.
Partners
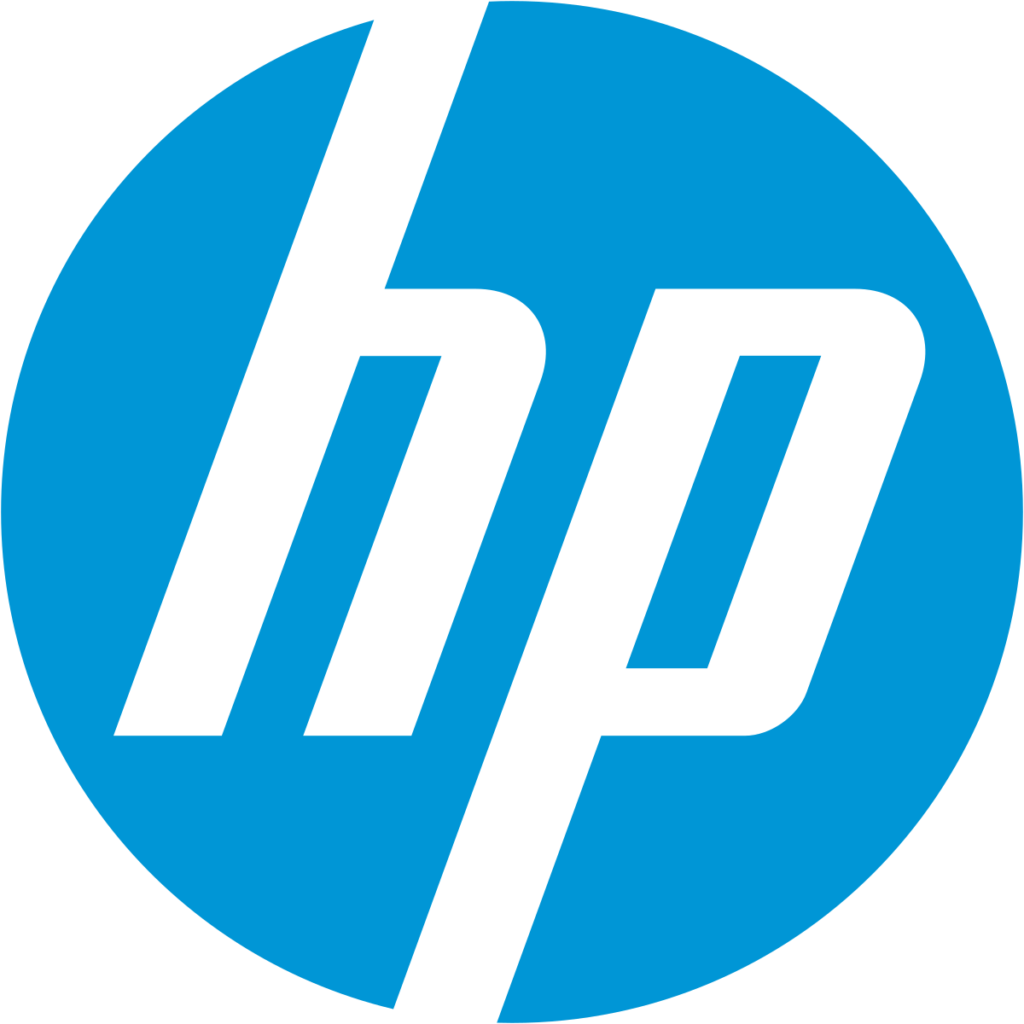
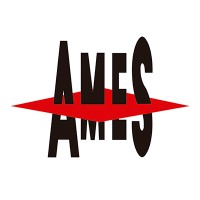
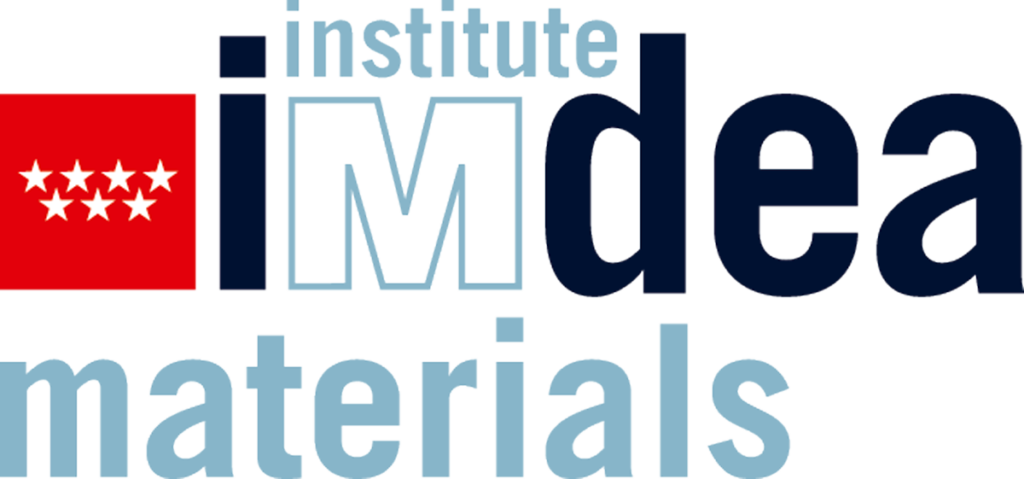
Funded by
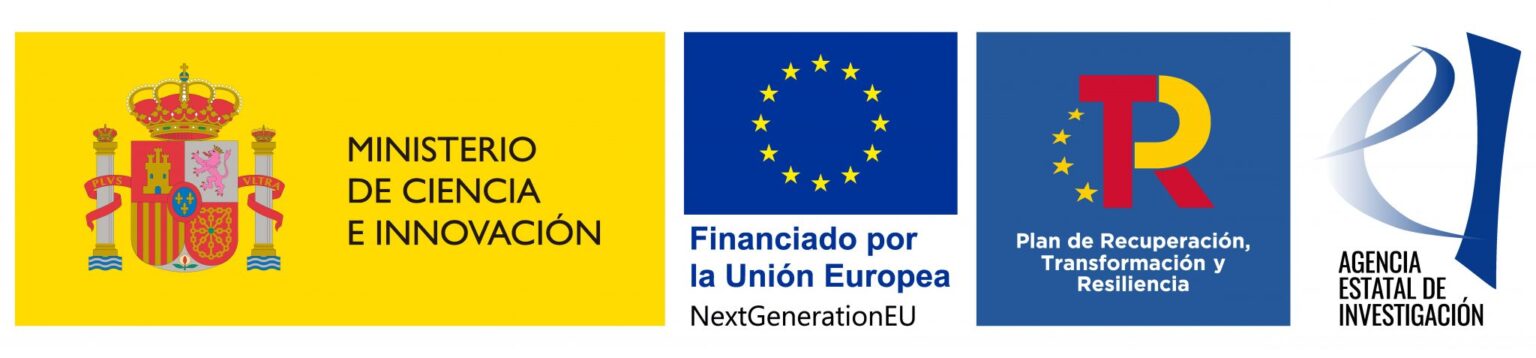
Proyecto CPP2022- 010002, financiado por MCIN/AEI/10.13039/ 501100011033 y por la Unión Europea “NextGenerationEU”/PRTR