Funding: Air Force Office of Scientific Research (AFOSR). U.S. Air Force Defense Research Sciences Program.
Region: International
Project period: 2019 – 2022
Principal Investigator: Claudio Faria Lopes (claudiosaul.lopes@imdea.org)
The AFRL (Air Force Research Laboratory) and IMDEA Materials are at the forefront of the science and engineering of structural composites by sharing a common view to the analysis of these materials which consists on a hierarchical bottom-up multiscale simulation approach that takes advantage of the natural separation of length scales between different composite entities (ply, laminate and component). This allows carrying out multiscale modelling by computing the properties of one entity (e.g. individual plies) and homogenizing the results into a constitutive model. This information is then passed to the simulations at the next higher length scale to determine the mechanical behavior of the larger entity (e.g. laminate). The computational micromechanics strategy to compute elastic, strength and fracture properties of composite plies relies on the properties of the basic constituents (fibers, matrix, and fiber-matrix interfaces) for different environmental conditions that need to be obtained from nano- and micromechanical characterization under the appropriate environment.
Within this strategy, involving many experimental and numerical techniques, there are capabilities between AFRL and IMDEA that are either complementary (e.g. constituent characterization) or redundant (e.g. damage modelling). Nevertheless, each of the modelling approaches have their advantages and contain particular features that could be transferred, and be of benefit, to the counterpart. Hence, a research collaboration between AFRL and IMDEA Materials is proposed that aims at:
i) promoting the sharing of experience and knowledge in experimental and computational micromechanics techniques to increase confidence on the methods and enhance each other’s capabilities;
ii) improving each other’s methods and approaches by implementing the best available features;
iii) progressing beyond the state-of-the-art by filling current gaps in knowledge of material properties, increasing material representativeness, improving experimental and computational methods, and extending simulation capabilities.
The topics of the collaboration towards establishing a full capability for multiscale virtual testing of composites include the development of nano- and micromechanical characterization test methods for the still unknown constituent material properties; the increase of realism in microstructural modelling; the cross-validation and cross-enhancement of damage propagation approaches; the development of experimental procedures for crack propagation assessment and; finally, the validation of the resulting computational approaches.
Partners
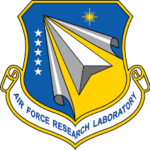
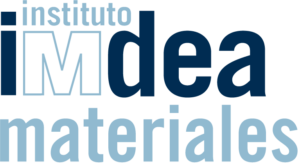
Funded by
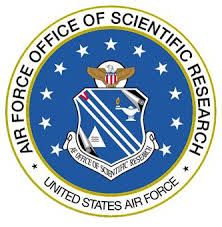