Software details
Software authors
Javier Segurado, Javier LLorca, Sergio Lucarini, Aitor Cruzado, Sarra Haouala, Vicente Herrera
Intellectual Property Rights
Copyright © 2012-2021 Fundación IMDEA Materiales and Universidad Politécnica de Madrid. All rights reserved
Opportunity
Commercial license through Digimat. Link
Software description
CAPSUL is a package of crystal plasticity and polycrystalline homogenization simulation tools. The package includes:
- A crystal plasticity constitutive model, aimed at predicting the elasto-plastic behaviour at the crystal level. The model incorporates physically-based and phenomenological implementations and both slip and twinning mechanisms are considered. Both monotonic response and cyclic behaviour are considered by the combination of different laws for isotropic hardening, kinematic hardening and cyclic softening. The model has already been successfully applied to simulate the mechanical performance of FCC (Al and Ni-based superalloys) and HCP alloys (Mg and Ti), including stress-strain curves and texture evolution under monotonic loading as well as crack initiation and fatigue life under cyclic loading. The model is programmed as a UMAT subroutine for Abaqus.
- A tool to generate finite element models representative of the actual alloy microstructure (grain size, shape and orientation distribution) using as input statistical data obtained from microscopy images.
- An inverse optimization tool to obtain the crystal plasticity model parameters from the result of a set of mechanical tests (both microtests or tests on polycrystals).
- A set of python scripts to generate cyclic loading conditions and to postprocess the results to obtain fatigue indicator parameters and other measures from microfields.
CAPSUL capabilities
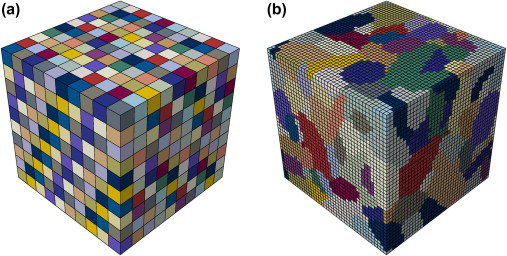
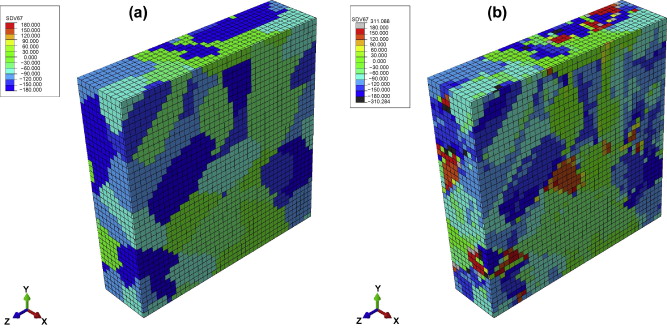
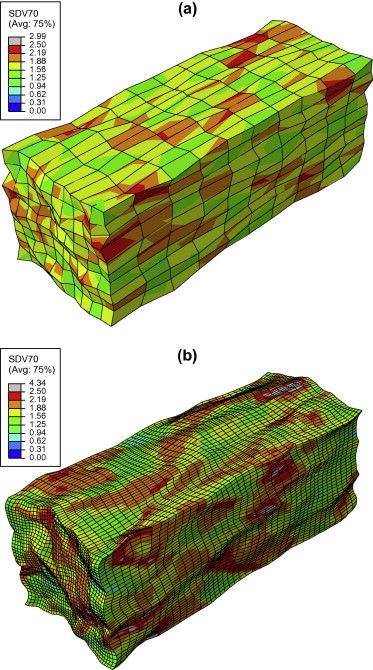
Relevant publications
[1] Simulation of the deformation of polycrystalline nanostructured Ti by computational homogenization.
Javier Segurado, Javier Llorca
Computational Materials Science, Volume 76, 2013, 3-11. DOI: https://doi.org/10.1016/j.commatsci.2013.03.008
Contact
Technology Transfer and Innovation Office, IMDEA Materials Institute
email: techtransfer.materials@imdea.org
telephone: +34 91 5493422