Researchers involved in the DOMMINIO project are moving ever closer to achieving their goal of creating a new digital method for the improved manufacturing of next-generation multifunctional airframe parts.
That’s according to DOMMINIO coordinator, Dr. Pablo Romero from AIMEN Technology Centre, who was speaking at the project’s penultimate General Assembly which took place at IMDEA Materials Institute (January 30-31).
DOMMINIO, a European research project funded by the Horizon 2020 research and innovation programme, involves 13 organisations from across Europe, including IMDEA Materials.
The project will officially wrap up in June 2024 after an intensive 3.5-year research effort to develop an innovative, data-driven methodology to design, manufacture, maintain and pre-certify components for the aviation industry.
Highlighting the fact that many of the project’s key demonstrators have already been manufactured, Dr. Romero said that the meeting had been highly productive in laying out DOMMINIO’s final sprint to the finish line.
“Our main objective between now and the end of the project will be to finalise the manufacture of the demos, to test them and to collect the information we need about how good the thermoplastic structures are compared to the thermosets,” he said.
“This relates back to the key mission of the project, which is to come up with new methodologies for maintenance, repair and overhaul of these critical components”.
“These new methodologies, which take into account that the structures will be intelligent and will be able to sense their own structural health, represent a paradigm shift from preventative maintenance to condition-based maintenance”.
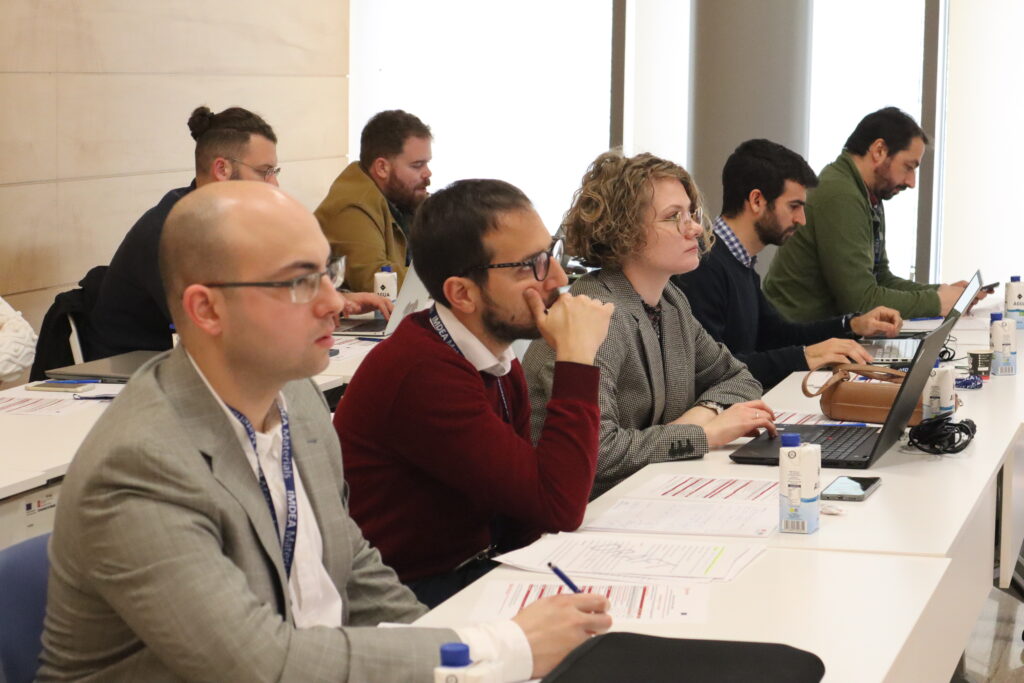
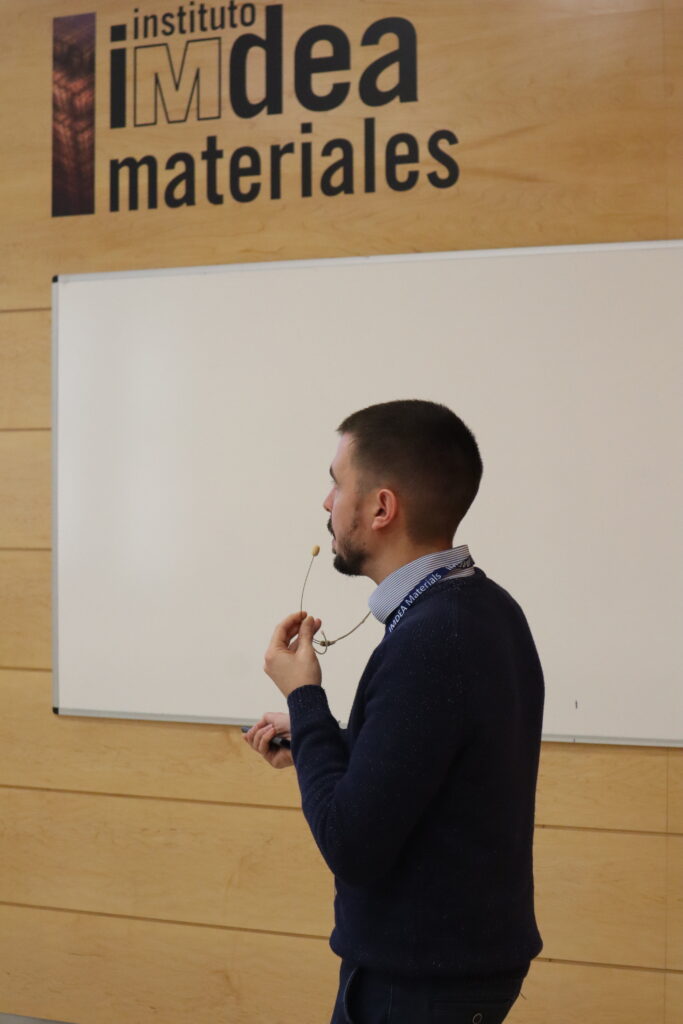
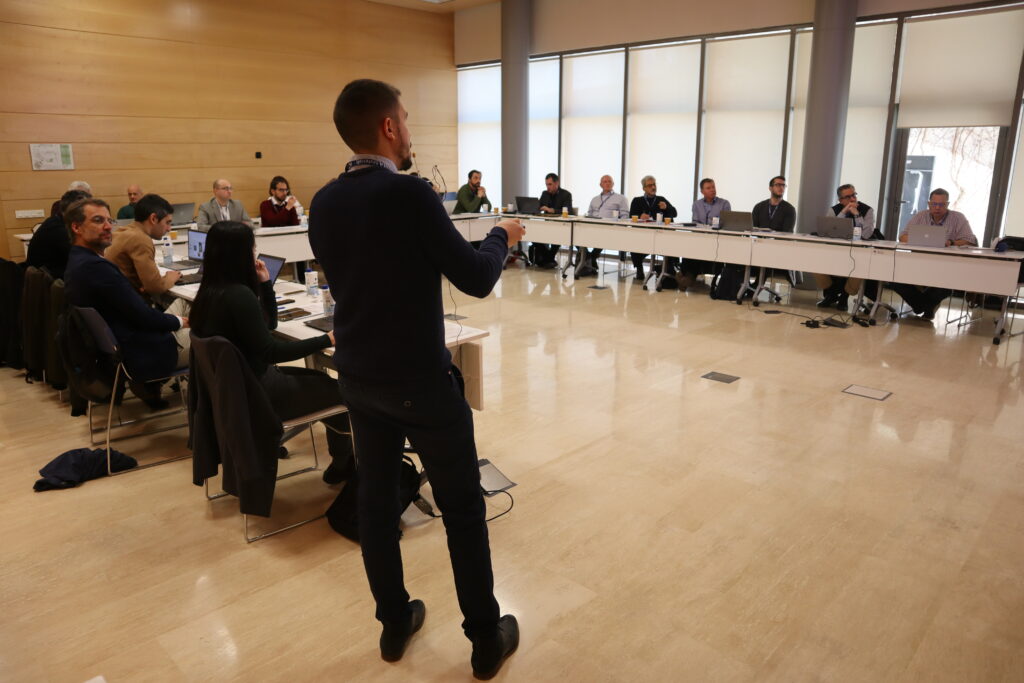
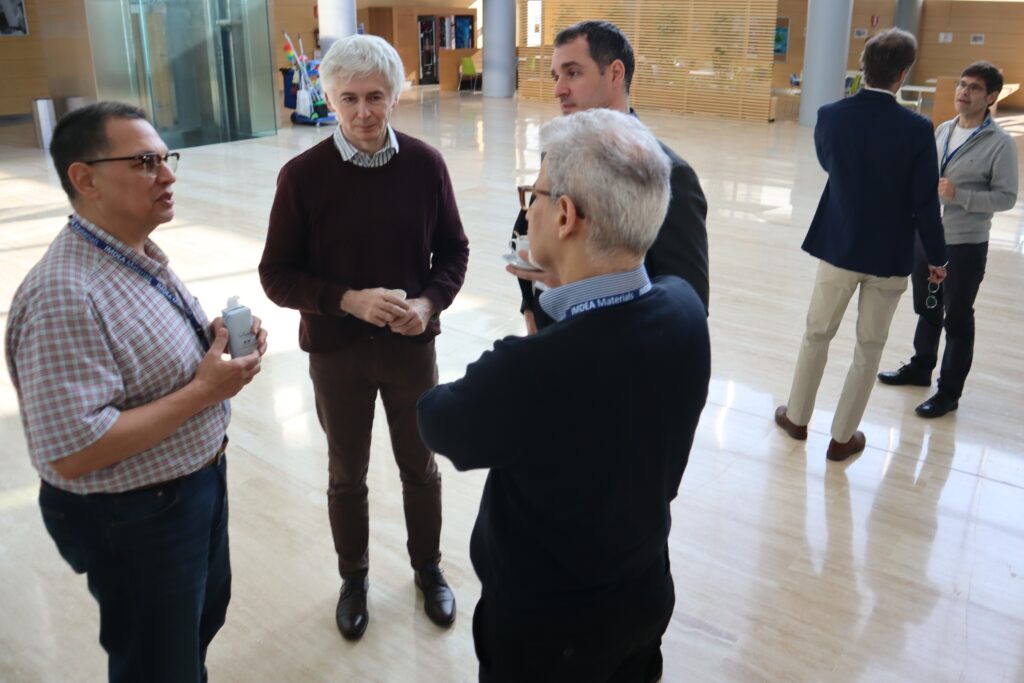
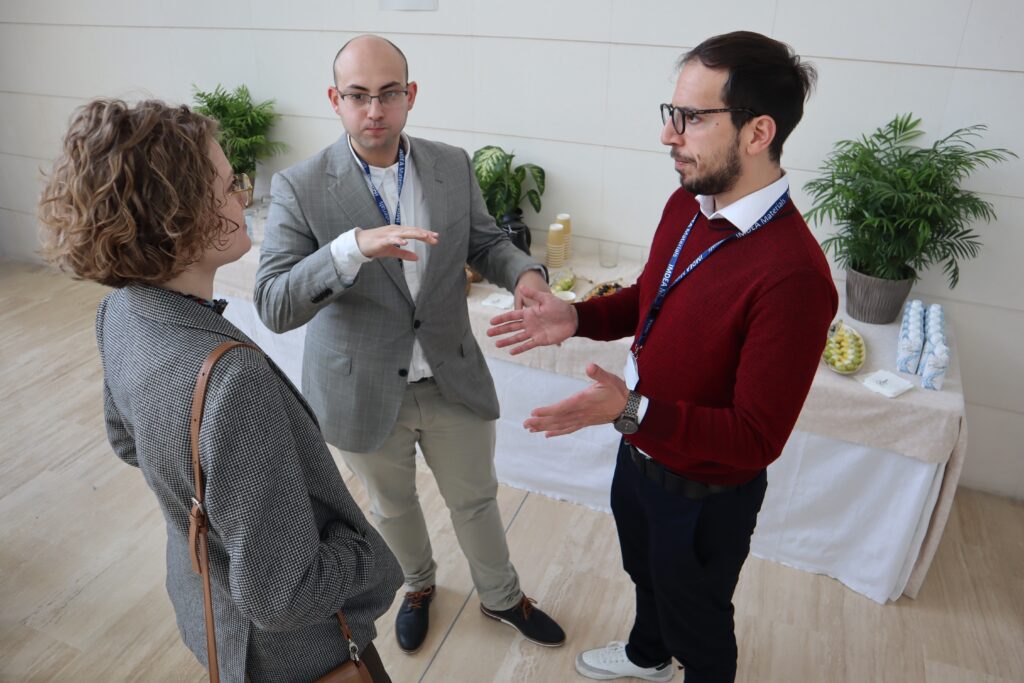
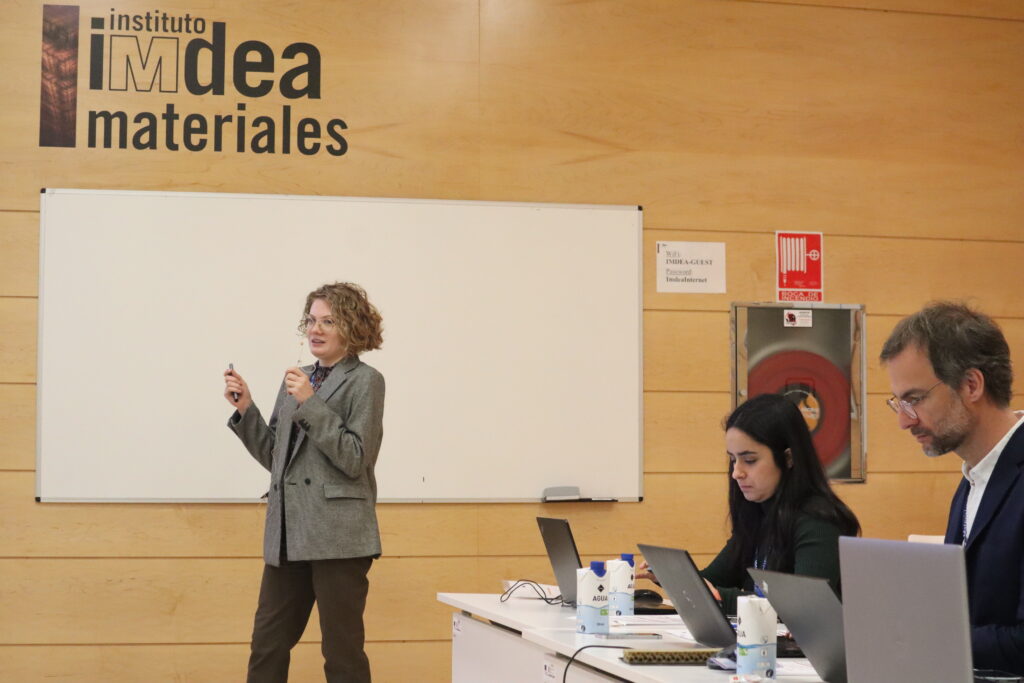
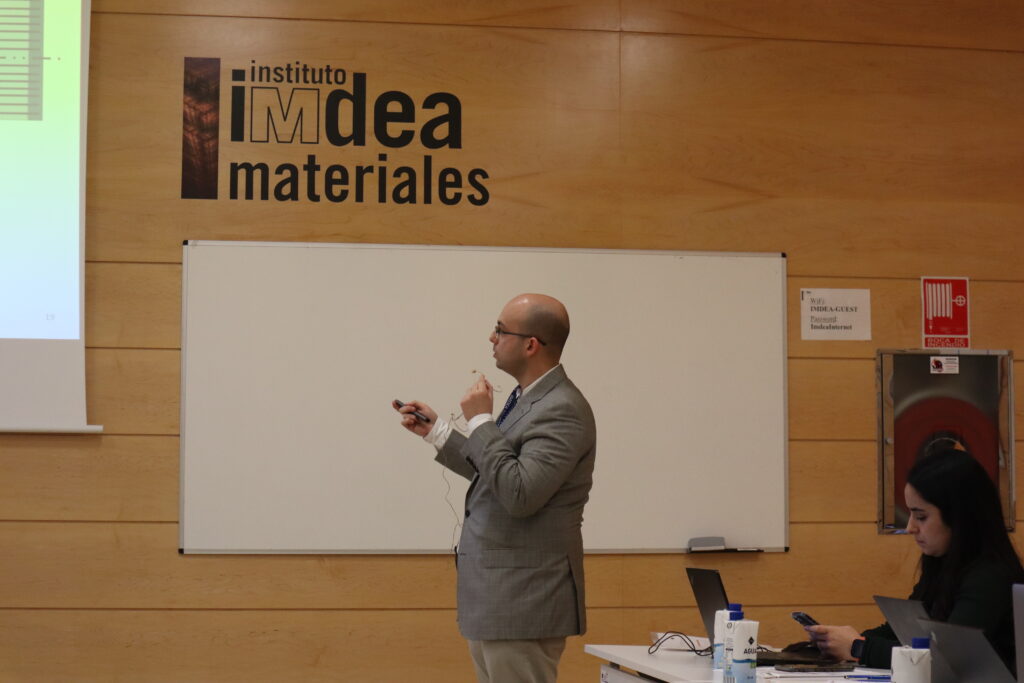
Condition-based maintenance is a methodology of equipment maintenance based on data collected in real-time during monitoring of the component and which is carried at the exact moment it is needed; before a critical failure occurs.
It has the advantage over more conventional maintenance techniques in that it minimises downtime and waste, offering greater maintenance and cost efficiency, as well as enhanced sustainability.
During the General Assembly, representatives from a majority of the consortium members were on hand to review the project’s three already completed work packages, and those which are still in development.
This included team members from AIMEN and IMDEA Materials, alongside those from the BAE Systems, INCAS, the National Technical University of Athens, ACITURRI, EASN Technology Innovation Services IRES and Dasel Systems.
There was a focus on the simulation on FFF (Fused Filament Fabrication) and AFP (Automated Fibre Placement) processes, and the new tools developed in relation to these designed to optimise the manufacturing process.
IMDEA Materials’ role within the project has been focused on the characterisation of the sensor technology and in the interpretation of the electronic data generated.
This has been carried out by the institute’s Structural Composites research group, led by Prof. Carlos González, and its’ Multifunctional Nanocomposites group led by Dr. Juan José Vilatela.
Drs. Davide Mocerino, Anastasia Mikhalchan and predoctoral researcher Moises Zarzoso are three of the IMDEA Materials team most actively involved in the project.
This project has received funding from the European Union’s Horizon 2020 research and innovation programme under grant agreement no. 101007022.
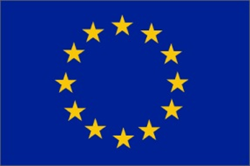