The use of polymer-based composite materials in aircraft structures has increased consistently in the last decades and today they represent up to 50% in weight for wings, fuselage sections and tail surfaces in the latest generation of commercial aircrafts. However, the use of such composites in other parts of the aircraft that could benefit from their low weight, such as the fan blades of engines and nacelles, is progressing, but at more subdued rate and this could be partially attributed to the lack of a general knowledge regarding the mechanical response of composite laminates under dynamic loading or impacts.
The dynamic behavior of structural composites is being investigated at IMDEA Materials within the DYNACOMP Project. The main aim of the DYNACOMP (Dynamic behavior of composite materials for next generation aero engines) training network is to set up a European Industrial Doctorate (EID) programme on the design of the next generation of structural composite materials for high strain rate applications (the next generation of aero engines mainly).
Within this project context, the dynamic behavior of prepregs laminates under interlaminar loading was studiedby using the wedge-insert fracture method (WIF) with double cantilever beam specimens (DCB) at high speed (up to 2000 mm/s) with a Gleeble 3800-GTC thermal-mechanical
physical system. The standard prepreg materials systems (e.g. IM7/8552) did not exhibit strain rate dependence in the range analyzed. However, last prepreg generation containing interlaminar tougheners (e.g. IM7/M91) showed a significant increase of the toughness with the loading speed up to some extent. X-ray tomograms of the tested specimens revealed irregular crack propagation caused by the presence of toughening particles at the interleaves. Finite element models using the cohesive approach were developed to check the consistency of the dynamic measurements and validate the data reduction methods used. Such models, once calibrated
with experimental results, can be used to ascertain the effect of strain rate on the mechanical performance of composite materials under dynamic loading conditions.
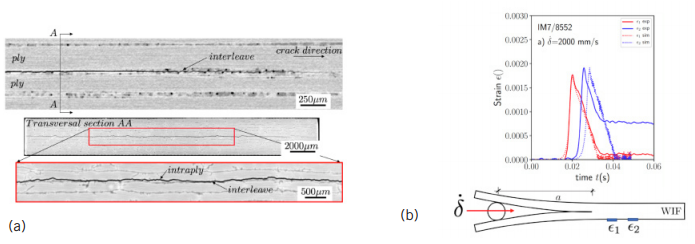
a) X-ray CT sections of the WIF specimen tested at high speed showing crack meandering due to the presence of secondary toughening particles, b) Model of the WIF specimen with comparison of the strain signals time evolution.
Dynamic characterisation of interlaminar fracture toughness in carbon fibre epoxy composite laminates.
M.A. Riezzo, M. Simmons, B. Russell, F. Sket, V. Martínez, C. González
Composites Part A: Applied Science and Manufacturing 126, 2019.
DOI: https://doi.org/10.1016/j.compositesa.2019.105597