- Researchers at IMDEA Materials Institute have developed a fire-resistant coating applicable to the aluminium panels commonly used in protective battery casings and housings.
- The coating has been shown to protect the panels from thermal penetration at temperatures of up to 1400℃.
IMDEA Materials Institute researchers have unveiled an innovative flame-retardant coating, effective at thicknesses of as low as 350 microns, which dramatically improves the fire resistance of the battery casings used in electric vehicles and aerospace.
Such a breakthrough promises to reduce the risks posed by phenomena such as thermal runaway in lithium-ion batteries, while also improving the applicability and performance of batteries in high-temperature scenarios.
The findings are the result of work from IMDEA Materials researchers Mr. Wei Tang and Mr. Yunhuan Liu, both members of the institute’s High-Performance Polymers and Fire Retardants group under the direction of Prof. Dr. De-Yi Wang.
In their research, the scientists conducted burn-through testing of both coated, and uncoated 3mm-aluminium plates, at temperatures of up to 1400°C.
This type of testing is of great importance in various industries, as it allows researchers to determine how long it takes for fire to penetrate a material, indicating its susceptibility to structural failure and potential hazards.
“What we found in the testing is that the uncoated aluminium substrates demonstrated a mere 135-second threshold before succumbing to thermal penetration at extreme temperatures,” revealed Mr. Tang.
“The same substrates with a coating of just 350 microns, however, displayed remarkable flame resistance, maintaining their structural integrity even after 15 minutes of high-temperature exposure. The testing also showed that the back temperature of the plate did not exceed 450℃,” he added.
This is well below aluminium’s melting point of approximately 660℃. While battery casings are not typically exposed to such extreme temperatures under normal operating conditions, this can happen in certain situations, particularly in aerospace applications or in industrial processes.
Without revealing the exact composition of the coating, researchers behind the breakthrough described it as a “functional polymer-based fire-resistant nanocoating”.
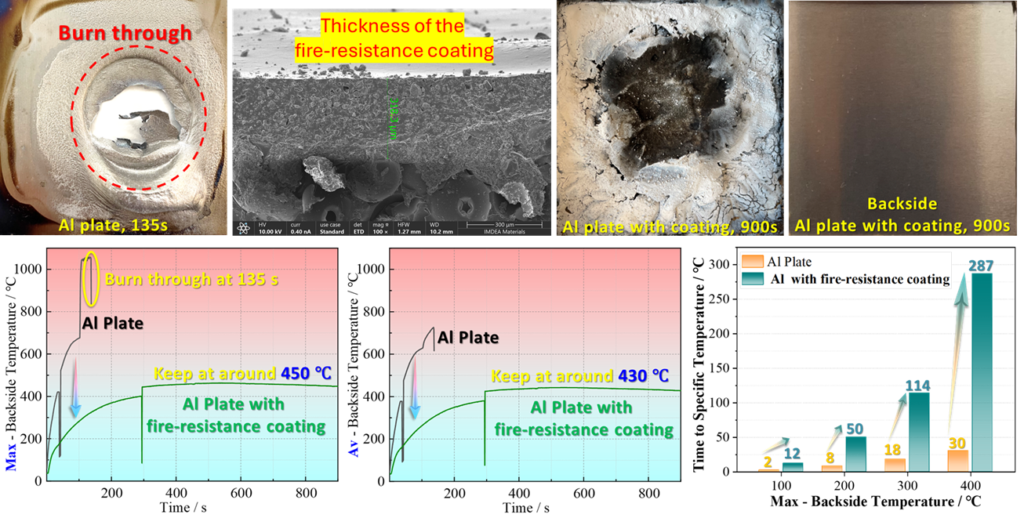
As well as aluminium, the coating has also been shown to be effective when applied to other materials, such as polymer foams, fibre-reinforced composites and steel, among others.
The secret to its efficacy lies in the fact that, when exposed to a direct flame, the coating immediately converts into a barrier formation on the material’s surface.
The barrier layer’s composition means that it remains very stable at high temperatures, and serves to insulate the underlying substrate from the direct heat of the flame.
Aside from its enhanced fire-retardant properties, the remarkable thinness of the coating required at just 0.35mm, also makes it more cost-effective and efficient for industrial applications.
“However, while we know that the coating is effective once applied, we still have work to do in terms of improving its processability,” acknowledged Mr. Liu.
“At the moment, this coating needs to be applied manually to achieve an appropriate dispersion and level of thickness on the material’s surface. However, we are in the process of optimising its processability for industrial manufacturing”.
“In addition, the coating’s production itself is quite simple and inexpensive, which makes it appealing in terms of scaling up its development to an industrial level”.