Patent details
Status
European patent filed
Inventors
Marcos Rodríguez Sánchez, María Teresa Pérez Prado, Damien Tourret, Adrián Dante Boccardo
Application number
EP24383248.2
Applicant
IMDEA Materials Institute
Priority date
18/11/2024
Transfer opportunity
License of technology
Summary
This invention introduces an innovative laser-based additive manufacturing device and method specifically designed for processing metallic glasses using laser powder bed fusion (LPBF, see Figure 1). The key challenge in manufacturing metallic glass parts lies in controlling their crystallisation, as these materials have a strong tendency to form crystalline regions during solidification, which can negatively affect their properties. The invention addresses this by integrating an adaptive scanning strategy that optimises LPBF process parameters before printing, ensuring an amorphous or controlled crystalline structure is formed.
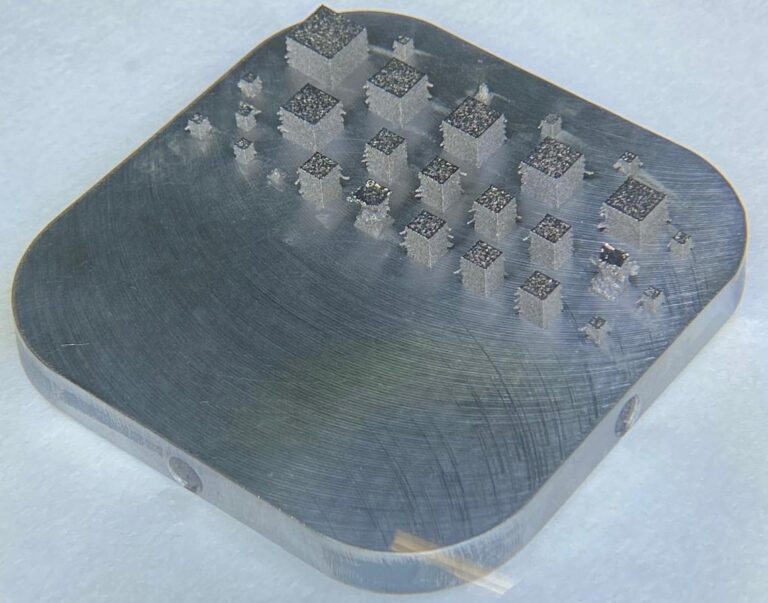
Figure 1: Substrates with printed samples.
By leveraging advanced simulations and artificial intelligence (AI)-driven optimisation, this method fine-tunes critical processing parameters such as laser power, scan speed, exposure time, and thermal cycles. The approach enhances the quality, consistency, and performance of metallic glass components, making it possible to manufacture larger and more complex structures than previously feasible. This breakthrough paves the way for new applications of metallic glasses in fields such as aerospace, biomedicine, precision engineering, and electronics, where their unique combination of high strength, corrosion resistance, and wear resistance is highly desirable.
Description
A major innovation in this invention is including a control unit that manages the entire process. This control unit integrates computer-aided design (CAD) modelling, process parameter selection, laser path optimisation, and real-time simulations (see Figure 2). Before printing, the system simulates the thermal behaviour of the metallic glass to predict and adjust key parameters such as cooling rate, solidification rate, and incubation time, ensuring the final printed object has the desired structural characteristics. The machine learning algorithms embedded in the software continuously improve the parameter selection process, leading to more efficient and reliable printing results over time.
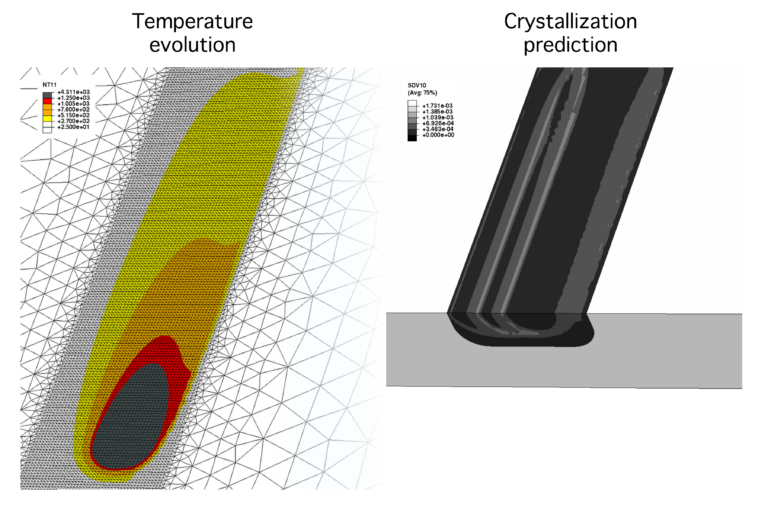
Figure 2: Temperature evolution and crystallisation prediction.
Advantages and Innovations
One of the most significant advantages of this patent is its ability to control crystallisation during additive manufacturing, which has long been a limiting factor in the application of metallic glasses. The optimisation of LPBF process parameters before printing allows for precise tuning of the material’s microstructure, ensuring improved mechanical and magnetic properties. This is particularly valuable for Fe-based metallic glasses, which are widely used in soft magnetic applications and advanced structural components.
Another key innovation is using AI-driven simulations to optimise process parameters, reducing the need for extensive trial-and-error experimentation. This lowers material waste and production costs and accelerates the development of high-performance parts. Additionally, the invention enables scalability, allowing the production of larger and more geometrically complex metallic glass components that were previously difficult to manufacture. This breakthrough expands the potential applications of metallic glasses beyond traditional small-scale uses, making them more viable for industrial and commercial applications.
Main Characteristics
The patented device and method are designed to work specifically with metallic
glass powders, particularly Fe-based alloys, which have excellent
mechanical strength, corrosion resistance, and wear resistance. The LPBF system
operates layer-by-layer, with each powder layer melting and solidified
under tightly controlled conditions. The process parameters, including laser
power, scan speed, exposure time, and hatch distance, are carefully
adjusted using a thermal-metallurgical model to ensure minimal crystallisation.
A defining feature of this system is its adaptive scanning strategy,
which tailors the laser’s movement across the powder bed to achieve optimal
cooling rates. The device’s control unit predicts and adjusts crystallisation
metrics in real time, ensuring that each printed part has a consistent
and reliable microstructure. The method suits applications requiring high-performance
metallic glass components, including biomedical implants, aerospace
structures, precision manufacturing tools, and advanced electronics. With
its ability to balance crystallisation control and process efficiency,
this invention represents a significant step forward in additive manufacturing
for metallic glasses.
Contact
Technology Transfer and Innovation Office, IMDEA Materials Institute
Email: techtransfer.materials@imdea.org
Telephone: +34 91 5493422