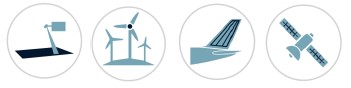
IMDEA Materials has recognized expertise on the design of alloys for high temperature, high strength and lightweight applications, which are suitable for the production of 3D printed components by laser-based or binder-jetting methods.
Previous works include the design of superalloys for turbine components, either in solid form or as lattice structures, as well as the definition of tuned compositions for high strength Al alloys with higher hardness than conventional wrought products.
IMDEA Materials is also a global leader on the design and optimization of Mg alloys for sustainable transportation and has successfully developed new intermetallics, high performance steels and high entropy alloys.
The competitive advantage of IMDEA Materials lies on its deep understanding of the processing-microstructure-mechanical property relationships, that is grounded on solid knowledge on physical metallurgy concepts, as well as on proven experience on microstructure and mechanical property characterization at all length scales.
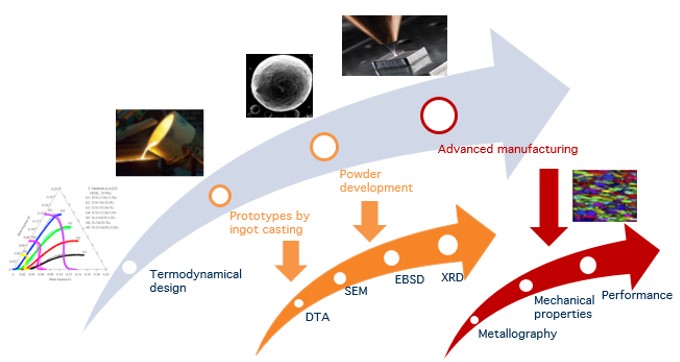
IMDEA Materials has a one-stop shop for the development of 3D-printed alloys. Experimental facilities (Fig. 1) include:
- Processing: ARCAST 200 arc melting and casting furnace furnished with laboratory scale gas atomizer
- 3D printing: AM400 Renishaw selective laser melting 3D printer
- Powder characterisation: Hall flowmeter, particle size analyzer, sieves
- Structure characterisation: X-ray diffractometer, FIB-FEGSEM and FEG-S/TEM microscopes
- Sample preparation, thermal treatments and mechanical testing at all length scales and conditions.
Experimental capabilities are complemented by a suite of simulation tools (Fig. 2). Computational models cover a broad range of length/time scales, from the atomic structure of interfaces to the macroscopic scale of entire components. These tools, coupled together and tailored to tackle specific technological challenges, include:
- Computational thermodynamics (CalPhaD), to predict the formation of different phases and calculate thermophysical properties of complex multicomponent alloys
- Macroscopic finite element analysis of AM processing nonlinear thermomechanics, to predict thermal profiles, residual stresses, and printed part distortions
- Phase-field modeling of microstructure development and microstructure evolution at the scale of the melt pool, to estimate key microstructural features
- Crystal plasticity theory and computational homogenization, to predict thermomechanical properties and performance (e.g. fatigue life) of heterogeneous microstructures.
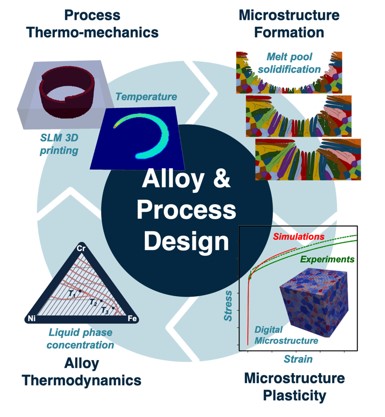