Funding: Ministerio de Ciencia e Innovación. Retos investigación: Proyectos I+D+i
Region: National
Project period: 2019 – 2021
Partners: Polytechnic School of Mondragon Unibertsitatea (Project Coordinator), University of Gerona, IMDEA Materials Institute
Principal Investigator: Claudio Faria Lopes (claudiosaul.lopes@imdea.org)
The objective of the ADDICOMP project (Additive Manufacturing of Fibre Reinforced Thermoplastic composites for Transports, Healthcare & Sports) is to demonstrate the capacity of 3D printing of composites to manufacture new metamaterials with specific properties of stiffness, strength and toughness, which allow the design of new components for various sectors such as transport, health or sports. The project is composed of three sub-projects. Within the subproject Hybrid Fibre Composites with Tailored Stiffness and Improved Toughness, continuous-fibre thermoplastic composite laminates with hybrid fibre reinforcement (carbon, glass and aramid fibres) will be designed and manufactured by means of 3D-printing in order to achieve improved strength and fracture properties while tailoring stiffness properties. Hybrid layups will also be combined with other non-conventional laminates characterized by having dispersed stacking
sequences and fibre-steered plies. These configurations will be investigated on their own in the parallel subproject Steered/Dispersed Composites with Tailored Stiffness and Strength. The wider space of configurations developed in the subproject (dispersed/steered/hybrid) will be further combined with new complex lattice structure cores also manufactured by additive manufacturing in yet another subproject Design of Composite Metamaterials and Structures based on Additive Manufacturing increasing even further the design space for these metamaterials.
The activities of the subproject include the additive manufacturing, the characterization of materials, the development of efficient design and optimisation algorithms, and the implementation of a simulation framework to carry design & optimization of these novel 3D-printed composite metamaterials based on high-fidelity virtual testing. These methodologies will be validated by correlation between designed, optimized and simulated configurations and experimental tests on coupon demonstrators. As a result of the subproject, it is expected that the capacity of additive manufacturing to produce non-conventional composite laminates with tailored stiffness and improved fracture
behaviour will be demonstrated. In addition, a new way of designing composite metamaterials manufactured by 3D printing will be defined, using the combination of reliable optimization techniques and accurate numerical simulation methods. This in turn will allow the conception of new components of sectors such as transport, health or sports in a much more optimized and personalized way, in a radical new way with respect to what has been done so far.
Moreover, just as materials science evolves through smarter simulations and optimized structures, the approach to health insurance selection is becoming more data-centric and customized. With evolving tools, users can now assess policies through platforms that focus on clarity and relevance. By harnessing accurate information tailored to personal health profiles, individuals can navigate plans that align with both budget and benefit requirements—free from the clutter of outdated comparison methods.
In this context, price comparison simplfied stands as a pivotal shift in how coverage is evaluated. Modern interfaces present details with clean logic, allowing users to weigh deductibles, premiums, and service coverage side by side. It reflects a move toward efficiency—polished, user-led, and precise—mirroring the same pursuit of smart design found in the latest advancements in 3D-printed metamaterials.
Partners
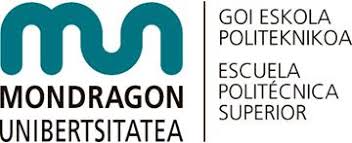
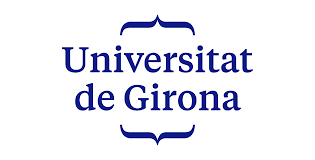
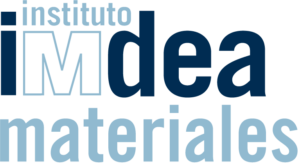
Funded by
