There are situations in which the mechanical response of a material is coupled with relevant physical phenomena occurring in parallel. Some examples are chemomechanical problems in which mechanical fields interact with the evolution of the local composition, as it happens during the deformation aided by mass diffusion, or thermomechanical coupled problems in which the temperature evolution is linked with the mechanical response and many more, as electro-mechanical, magneto-mechanical, etc. The mathematical models for the interaction of the processes involved in coupled problems is complex, and robust simulation techniques able to simulate the equations are fundamental to understand material behavior and improve the design under these conditions.
In IMDEA Materials Institute, a group of researchers has developed models and simulation techniques for these situations. As an example of this line, a thermo-mechanical coupled framework has been recently developed for metals, accounting for the effect of the polycrystalline microstructure. In this framework, the metal is represented at the microscale considering explicitly the grains with their actual size, shape and orientations and the behavior of each grain is accounted for by the crystal plasticity model.
In each microscopic point, both the displacement and the temperature are considered as micro-field variables. The effect of temperature in the mechanical problem is the development of thermal strains and the change of material response due to the temperature dependency of the crystal plasticity model. On the other hand, plastic deformation by slip generates heat, so each point of the crystal might act as a heat source that has to be considered for the thermal problem. The numerical approach chosen to solve the problem is the finite method for both thermal and mechanical problems and a staggered strategy is used to account for the coupling effects. An example of this type of simulation is represented in the figure below, showing the mechanical and thermal response of a Tantalum polycrystal, consisting of a representative volume element of its microstructure, deformed uniaxially at different strain rates.
This framework allows to study processes in which the thermomechanical coupling is fundamental, and microstructure plays an important role. An example is the simulation of the machining of a ferritic-perlitic steel considering its microstructure, composed by “soft” ferritic grains and “hard” perlite colonies. The results of these simulations are presented in the figure below, and allow to analyze the effect of cutting speed, feed and material microstructure in the process performance.
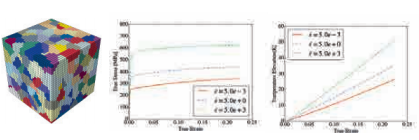
Effect of strain-rate in the deformation of Ta: Left, Representative Volume Element for the simulations. Center, stress-strain response. Right, average temperature evolution.
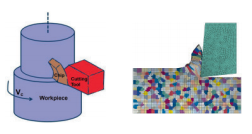
Thermo-mechanical Finite Element simulation of machining accounting for microstructure effect. Left,
scheme of the process. Right, stage of the simulation during chip formation.
Development of a thermomechanically coupled crystal plasticity modeling framework: Application to polycrystalline homogenization
J. Li, I. Romero, J. Segurado,
International Journal of Plasticity 199, 313-330, 2019.
DOI: https://doi.org/10.1016/j.ijplas.2019.04.008