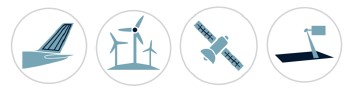
Due to the rapid growth in the use of composite materials, environmental concerns have become an increasingly influential topic, making recyclability of composite materials a key issue. Furthermore, several related EU laws have been passed to minimize the environmental impact of composite structures and to make rational use of landfills. However, the number of composites currently recycled is less than 5% of the total amount produced requiring efforts to reuse such kind of waste materials in a circular economy.
IMDEA Materials has developed technologies to manufacture 3D printed composite parts made with recycled fibers obtained from structural composites scraps (Fig. 1). The process starts with the recovery of the carbon/glass fibers from cured composite parts or prepreg scraps. It consists of two subsequent steps: a thermolysis or pyrolysis, followed by a gasification or oxidation. In the first one, the separation fibre/resin takes place; in the second stage, the char deposited on the surface of the fibres is removed. After that process, the recovered fiber is subjected to milling to produce short fibers. IMDEA Materials has the possibility to manufacture polymer pellets containing different fiber charges by means of extrusion. These pellets can be used for injection moulding and production of 3D printer filaments (3DEvo) with a variety of diameters and polymers (typically PLA). Filament fused deposition systems as well as advanced short and long fiber 3D printers are available. This capability in combination with expertise in design and optimization of structural composite parts by means of advanced finite element modelling has the potential to be fully exploited in automotive, aerospace and other sectors to produce recycled parts with tailored properties.
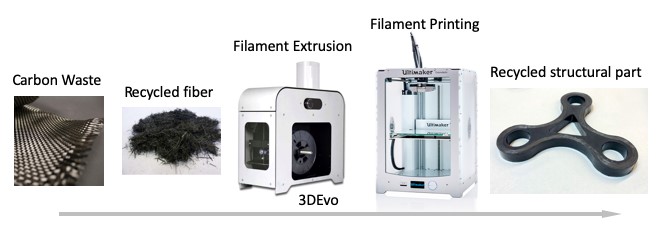