- The innovative nature of this breakthrough lies in the fusion of nanoplatelets of graphene oxide (GO) with a poly(lactic acid) (PLA)-based textile fabric through a streamlined one-step spray coating process.
- The research is outlined in the recently published article, Graphene Oxide/Polylactic Acid-Based Face Mask to Combat H3N2: a strategy against Influenza.
In the relentless battle against airborne viruses, researchers from IMDEA Materials Institute, Rey Juan Carlos University (URJC) and the University of Valladolid (UVa), have developed a new spray coating to improve the antiviral efficacy of personal protective equipment, notably face masks.
GO possesses inherent antiviral properties due to its unique chemical structure, which can serve to render viruses non-infectious while prohibiting viral replication and propagation.
Importantly, the integration of the GO spray coating in the latest research was also shown to have no negative effect on the structural integrity or air permeability of the textile, thereby ensuring comfort and breathability for the wearer.
“The antiviral properties of GO in solutions have been proved previously,” explained IMDEA Materials researcher Jimena de la Vega, one of the authors behind the study.
“However, this is the first time that an antiviral GO solution has been directly integrated into a biodegradable fabric to create a more effective and more environmentally friendly material for face masks”.
“The pores of the fabric that we have used for these masks are also smaller than the size of the viral droplets. That means they prevent these droplets from being inhaled by the wearer, while the breathability of the mask is unaffected.”
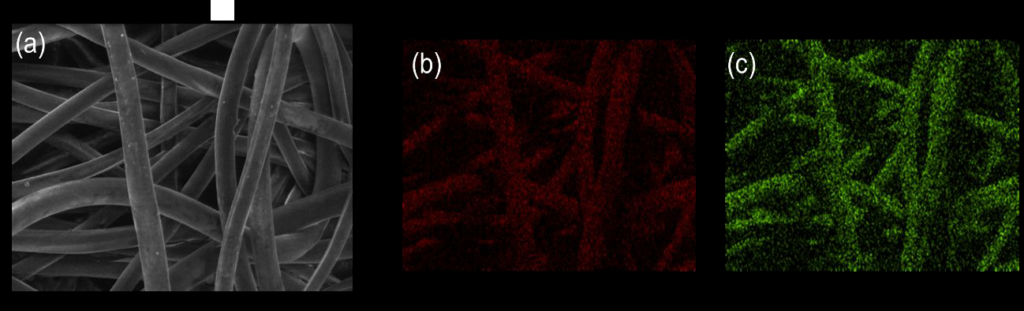
(c) shows EDS mapping with the presence of Carbon and Oxygen, respectively.
Personal protective equipment has become an indispensable tool in mitigating the spread of infectious diseases, especially in the wake of the COVID-19 pandemic. Airborne viruses pose a
persistent threat to public health, with the potential to precipitate future outbreaks.
Traditional face masks primarily rely on filtration mechanisms to intercept airborne particles. However, their efficacy can be significantly bolstered by integrating antiviral coatings, thereby inhibiting viral replication and transmission.
The incorporation of GO particles into the mask fabric, also elevates the textile’s water contact angle, potentially thwarting the infiltration of droplets laden with infectious agents.
The research team behind the study includes Dr. Antonio Vázquez-López and Profs. Silvia Prolongo and Ignacio Collado from URJC, Profs. Pedro Prádanos and Francisco Javier Carmona (UVa), and Jimena de la Vega and Prof. Dr. De-Yi Wang from IMDEA Materials.
Dr. Vázquez-López, himself a former IMDEA Materials researcher, said he had found inspiration for the breakthrough from the common practice of using wood ash as a pesticide to protect crops.
“While the effectiveness of this practice is partially a myth, from this starting point I was led to the idea of using carbonaceous materials for their antibacterial and antiviral qualities,” he explained. “Ideally, these materials had to be abundant and non-toxic.”
“GO was one of several additives with these properties that was tried during this research and was one of the easiest to work with. However, GO dispersion can be quite difficult. Luckily, we were able to work with the Spanish company Antolin which has experience in providing GO in water suspension, which greatly simplified the process.”
“There is existing research on using graphene or carbon nanotubes for antiviral coatings, but as far as I am aware, nothing related to using GO, and certainly not combined with a recyclable PLA-based fabric.”
The utilisation of an environmentally sustainable material such as PLA, underscores a commitment to addressing not only public health concerns in face mask production, but also environmental sustainability challenges.
Meanwhile, Dr. Vázquez-López was also confident of the potential scalability of the enhanced antiviral mask’s fabrication process.
“One of my objectives with this research was to be able to automate the process as much as possible to streamline its manufacture,” he said. “A water-dispersed GO solution is easy to work with, and can be easily applied to the material at an industrial level.”