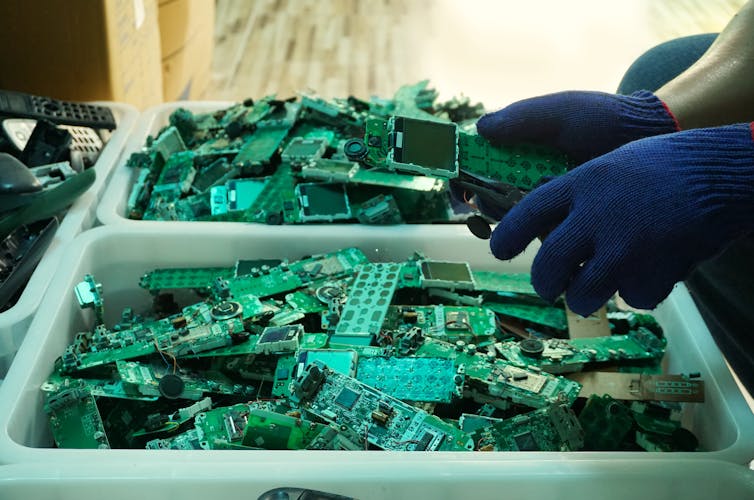
José Manuel Torralba, IMDEA MATERIALES; Alberto Meza, IMDEA and Damien Tourret, IMDEA
Although the amounts of precious metals like gold in electronic waste are very small (on the order of 300 grams per ton), obtaining a kilogram of gold still only requires between three and four tons of smartphones, compared to the 200 tons needed to process a gold ore (usually with concentrations in parts per million). With that being the case, it seems worthwhile to recycle all the world’s waste, doesn’t it?
However, of the 53.6 million tons of electronic waste generated in 2019 (projected to reach 77.4 million tons by 2030), only 17.4% was recycled. The rest is discarded, and it is suffocating us.
We have an imaginative proposal to recycle and profitably utilize the array of metals in electronic waste. It’s not nonsense or a delusion; it’s connecting the dots with the scientific knowledge we have and betting on revolutionizing the future starting today.
The treasure buried in electronic waste
Between 30-32% of electronic waste by weight consists of metals. It turns out that we have a large supermarket of metals at our disposal, including precious rare earth elements.
The combination of metals found in many types of waste include copper, nickel, or iron-based superalloys. Many of them contain highly valued metals such as aluminum, lithium, cobalt, and silicon, not to mention the previously mentioned rare earths and gold.
The following table shows the percentage of metals in various electronic devices. To give us an idea of what is lost when we bury our CPU, mobile phone, or a lithium battery.
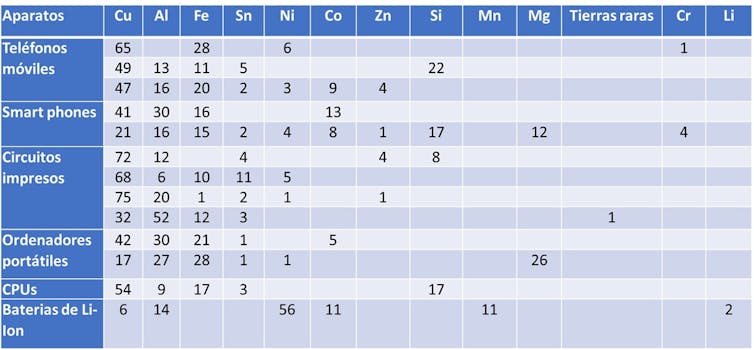
In a continent like Europe, where we have such stringent regulation on critical and strategic metals, and where we import the majority of what we consume from African countries, South America, China, or Russia, how is it possible that we are not fully taking advantage of this mine that we have in electronic waste?
Only copper, aluminum, nickel, and gold are of interest
The answer lies in the fact that companies involved in electronic waste recycling focus their efforts on recovering only the most precious metals. In other words, they engage in selective recovery, only targeting copper, nickel, aluminum, and, of course, gold, while disregarding the rest.
If we were to recycle the other metals, it would require a similarly selective recycling process for each one, which is expensive and complex. Often, the cost doesn’t justify such an approach.
Additionally, the extraction processes, usually involving leaching, are not environmentally friendly. A typical electronic waste recovery process (such as from printed circuit boards) involves, after separating the metallic part, an operation to separate iron (via magnetic separation), leaching to separate copper, another leaching step for precious metals, and, in the best-case scenario, an additional step for nickel. The remaining minor metals are typically discarded.
For all these reasons, electronic waste recycling fails to capture the vast majority of its potential value.
The imaginative proposal: everything at once.
But, what if we recover all of them at once?
The separation of the entire set of metals from a specific source of electronic waste would involve a single leaching operation (two, in the case of wanting to separate any high-value metal like gold), and we would make use of all the metals present in the waste. In a faster and cheaper way, we could recover the entirety of the metals.
Why isn’t this done?
The current answer is that the material resulting from a combined recycling is not useful, or it is of very limited use. We would obtain a complex alloy without a specific practical application. However, that is only the situation as of today. Let’s move forward.
We recently published a study in Intermetallics that demonstrates that by mixing alloys equivalent to those found in electronic waste (if recovered in their entirety) in the right proportions, high-performance high-entropy alloys can be produced. Is this good? Yes, it is very good.
The material of the future: high-entropy alloys.
The resulting materials, high-entropy alloys, can compete with the best-known alloys in areas such as high temperatures, magnetic properties, hydrogen storage, etc. They are emerging as the material of the future, and substantial funds are being invested in researching them.
They could represent a significant quantitative leap in various applications, from magnetic to structural ones. However, the excessive use of critical and strategic metals in their development is hindering their industrial implementation. With the development of this idea, we would achieve a double success: recycling all electronic waste and promoting the promising high-entropy alloys.
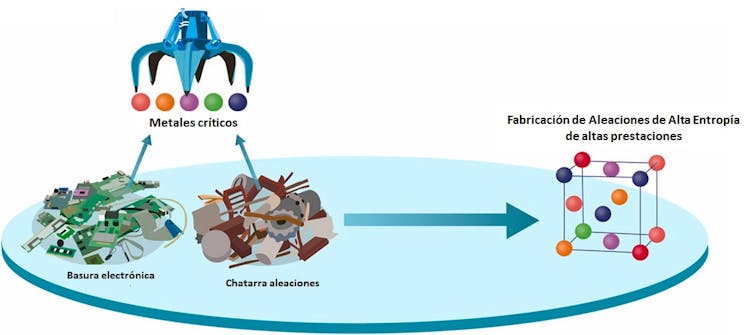
Summary of the recycling process to obtain high-entropy alloys. Sciencedirect
The squaring of the circle
Not without the industry.
It would be necessary to create a market that could consume alloys extracted from electronic waste, with all its elements at once. This would also imply that recycling would be more profitable, as total extraction of all metals is simpler and cheaper than the selective recovery of one or more metals.
It is challenging for a mass production manufacturer to commit to an alloy that relies on one or more metals for which a continuous supply cannot be guaranteed. However, by using electronic waste as a source, we would have solved this problem.
On one hand, we address a global scale issue through a cheaper and more efficient recycling process, and on the other hand, we drive the development of high-performance alloys (high-entropy alloys) without the need to depend on the supply of critical or strategic metals: squaring the circle.
José Manuel Torralba, Professor at the Carlos III University in Madrid, IMDEA MATERIALES; Alberto Meza, Postdoctoral Researcher, IMDEA y Damien Tourret, Senior Researcher in Materials Science & Engineering, IMDEA.
This article was originally published in The Conversation. Read the original (content in Spanish).