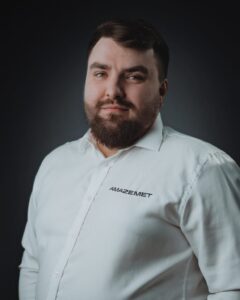
Tomasz Choma is an Application Engineer at AMAZEMET, one of two new partners to join the BIOMET4D consortium in 2024 alongside RWTH Aachen University Hospital. Read more about these new additions at the BIOMET4D website. In this interview, we speak with him about AMAZEMET’s role in BIOMET4D as well as the skills and expertise in additive manufacturing that they bring to the project and more.
Tomasz, to begin this interview, can you start by briefly explaining how AMAZEMET came to join the BIOMET4D project?
Tomasz: Our journey to BIOMET4D began through our longstanding relationship with IMDEA Materials Institute, particularly with Professor Javier LLorca, the Institute’s Scientific Director. Over the years, we’ve collaborated extensively, including on a Marie Skłodowska-Curie Action (MSCA) project between Warsaw University of Technology and IMDEA Materials, focusing on magnesium (Mg) and zinc (Zn)-based alloys. When the HOP-ON call presented an opportunity to join the ongoing EIC Pathfinder project BIOMET4D, we saw it as a natural fit. Our role as a consortium member is centered on leveraging our ultrasonic atomisation technology to manufacture high-quality powders. The flexibility of this technology, coupled with our expertise in alloy development, allows us to contribute effectively to the project’s goals.
Can you explain what AMAZEMET brings to BIOMET4D in terms of your expertise in additive manufacturing development and production?
Tomasz: At AMAZEMET, our primary objective is to produce high-quality powders tailored for Laser Powder Bed Fusion (LPBF). As a company with extensive experience in designing, manufacturing, and deploying ultrasonic atomizers – over 60 installations worldwide – we have developed deep expertise in powder production. Additionally, we aim to address the recycling challenges of multi-material powders generated during 3D printing processes. These mixtures, often treated as waste, can be repurposed through sustainable recycling methods, aligning with the principles of the circular economy and environmental sustainability.
Following on from this question more specifically, if you were to highlight one or two key objectives that you would like to see AMAZEMET achieve as a part of this project, what would they be?
Tomasz: Our first key objective is to refine the production process to produce Mg and Zn-based powders with the characteristics required for achieving superior quality in LPBF processes and ensuring the printed parts meet stringent performance standards. Secondly, we aim to develop an efficient separation process for the multi-material powder mixtures generated during 3D printing. Multi-material printing often results in mixed powders due to selective feeding. Addressing this challenge is critical to maintaining the sustainability and circular economy associated with additive manufacturing. By designing a method to separate and recycle these powders, we hope to enhance resource efficiency in the field.
For you personally, as one of the AMAZEMET team members involved in BIOMET4D, what is it that interests or excites you about this project?
Tomasz: As a materials engineer specialising in metals, powder production, and metal additive manufacturing, this project offers an exciting opportunity to explore the medical field. It’s fascinating to delve into the challenges of implants, learn about the rigorous testing procedures, and understand the specific requirements for medical devices. This exposure broadens our perspective and allows us to contribute to advancements in this critical sector. More broadly, additive manufacturing holds tremendous potential in revolutionising medical implants and devices. Its ability to create patient-specific solutions, intricate geometries, and complex designs is unmatched. Moreover, it supports the use of advanced materials, enabling implants with enhanced biocompatibility, mechanical performance, and longevity. The technology’s versatility also promotes innovation in drug delivery systems and surgical tools, driving the next generation of medical advancements.
Finally, I understand that this is not AMAZEMET’s first collaboration with IMDEA Materials. Can you please talk about the wider collaboration that exists between AMAZEMET and IMDEA?
Tomasz: That’s correct. Our partnership with IMDEA Materials spans multiple levels. Currently, we are collaborating on two Pathfinder projects, including BIOMET4D. The second project is AM2SoftMag that focuses on Additive Manufacturing of soft magnetic Bulk Metallic Glasses for electrical motors. Beyond formal calls, we have established a strong relationship through joint research initiatives and knowledge exchange. Additionally, AMAZEMET is a member of IMDEA’s Industrial Advisory Board, which fosters dialogue between industry and academia. This relationship has been mutually enriching, enabling us to contribute our expertise while benefiting from IMDEA’s cutting-edge research capabilities.
Thank you very much Tomasz for taking the time to speak with BIOMET4D today!