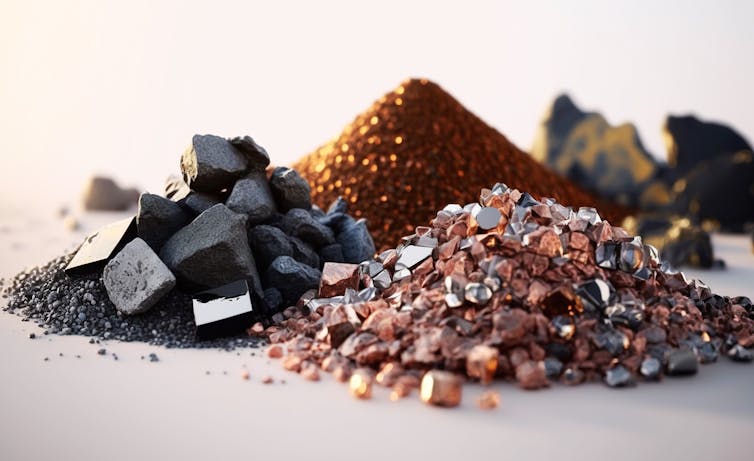
José Manuel Torralba, IMDEA MATERIALS y Miguel Ángel Rodiel, IMDEA
Replacing fossil fuels brings with it challenges and side effects that must be considered by all parties involved in Europe’s energy transition, vital to our future. To begin with, however, we must ask one seemingly obvious, but often forgotten question: do we have the materials to make the change?
The side effects of green technologies
The energy transition focuses on what are known as green technologies, primarily wind, solar cells, and batteries.
We know, for example, that the amount of CO₂ generated by solar or wind energy is 40-50 times lower than that generated by gas or coal-based energy. However, manufacturing the necessary devices to implement these green technologies is not as sustainable as it requires enormous quantities of metals produced through CO₂-intensive processes. This is known as the rebound effect.
More specifically, one of the main CO₂ emitters is steel production. If we acknowledge that wind and solar energies consume more than twice the amount of steel compared to coal or gas, the CO₂ emitted due to steel manufacturing using current metallurgical techniques will be very high during the construction phase of the new facilities.
The case of electric cars
Let’s focus on electric vehicles. The amount of CO₂ emitted by an electric vehicle over its lifetime is, on average, half that of an internal combustion engine vehicle. However, if the goal is to completely replace the existing vehicle fleet (rather than significantly reduce it), it’s important to understand that the manufacturing of these electric cars requires up to 6 times more materials than the production of a non-electric vehicle. Therefore, this is another rebound effect that we should try to minimise in the current wave of electric car manufacturing.
Furthermore, to assess the benefits of transitioning to electric vehicles, we need to analyze whether the technologies generating electricity to charge them are truly green and to what extent.
In terms of numbers, the CO₂ emitted throughout the life cycle of an electric car, including manufacturing, is approximately 20 tCO2eq, while for an internal combustion engine car, it’s about 42 tCO2eq. For vehicles charged with 100% renewable electricity, this figure could drop to around 10 tCO2eq. However, it rises to 40 tCO2eq if the electricity is generated from fossil fuel sources.
Therefore, as the electric vehicle fleet grows, we must ensure that the proportion of electricity coming from renewable sources increases proportionally if we intend for it to be a genuine advantage over internal combustion engines.
Only by introducing sustainable manufacturing practices from the outset of each of these technologies can we minimise this rebound effect and ensure the lowest CO₂ emissions throughout the life cycle of these new clean energy technologies.
The scarcity of raw materials
The second problem is possibly the most complex to solve: the scarcity of raw materials.
Let’s consider the amount of metals required to meet the demand for electric motors needed to fulfill the European Union’s mandate that internal combustion engine cars cannot be sold after 2035.
There are at least 6 fundamental metals – zinc, nickel, lithium, cobalt, silicon, and vanadium – for which there are currently not enough global reserves to meet this initial wave of demand. And there are others, like iron and copper, that would experience such a significant increase in demand that their production could become a serious problem.
To put it in perspective, humanity has consumed 880 million tons of copper in the last 6,000 years. In just the next 25 years, and solely to meet the demand for the electric motors that would need to be manufactured, we will need over 700 million tons of this metal. In other words, we will need nearly the same amount in 25 years as we have used in the last 6,000.
How to ensure that steel ceases to be a problem
The energy transition requires not only political or social will, but also a significant technological revolution and a radical transformation in the way we manufacture or process the involved raw materials.
Let’s revisit the case of steel manufacturing, one of the main ‘culprits’ of global CO₂ emissions (responsible for 20-25% of total industrial CO₂ emissions).
If we were to use green hydrogen in the production of steel instead of coke, and if we brought production centers closer to raw materials (considering that a significant source of emissions in steel production is the transportation of its raw materials), we could remove steel manufacturing from the list of problems.
The same policy should be applied to any raw material involved in energy production.
80% of electronic waste materials are not recycled
Of strategic importance, as established by the European Union, is the search for alternatives to critical materials.
Similarly, we must address the supply of raw materials in a diversified and sustainable manner, promoting efficiency in their use and increasing recycling to support the energy transition. To understand the scale of the problem, nearly 80% of the hundreds of thousands of tons of metals in electronic waste still remain unrecycled today.
In order to provide solutions, it is necessary to acknowledge the problems. Policy changes must be accompanied by clear investment strategies and the necessary time for technologies to adapt to the changing needs.
Without a doubt, we must invest in research and development to adapt many of these technologies to the urgent sustainability needs of the system. If we fail to do so, we will not succeed.
José Manuel Torralba, Professor in the Carlos III University Madrid, IMDEA MATERIALES and Miguel Ángel Rodiel, Technology Director, IMDEA MATERIALES.
This article was originally published in The Conversation. Read the original.
<iframe src=”https://counter.theconversation.com/content/213087/count.gif?distributor=republish-lightbox-advanced” width=”1″ height=”1″ style=”border: none !important” referrerpolicy=”no-referrer-when-downgrade”></iframe>