- Floatech has a patented and scalable process for manufacturing 100% silicon anodes for the next generation of lithium batteries.
- A spin-off of IMDEA Materials Institute, Floatech has already attracted interest from industrial investors and expects to get its first pilot plant up and running in 2023.
Floatech, a Madrid-based spin-off of IMDEA Materials Institute, plans to open its first pilot plant for the manufacture of silicon anodes this year.
Silicon anodes will be vital for the next generation of lithium ion batteries (LIBs) that will power the electric vehicles of the future. The international market for these LIB anodes for electric mobility is valued at more than €36 billion, and is forecast to have a year-on-year growth of 18% for the period 2022-2032.
Currently, Floatech’s production of anodes, and the silicon nanowires required, is carried out under IMDEA Materials’ incubation program, where the startup was born 2 years ago. The company is dedicated to the commercialization of its patented electrodes to customers in both Europe and the United States.
Floatech has already attracted the interest of investors looking to create a joint venture focused on the production of silicon anodes on an industrial scale and the start-up of manufacturing plants to supply them.
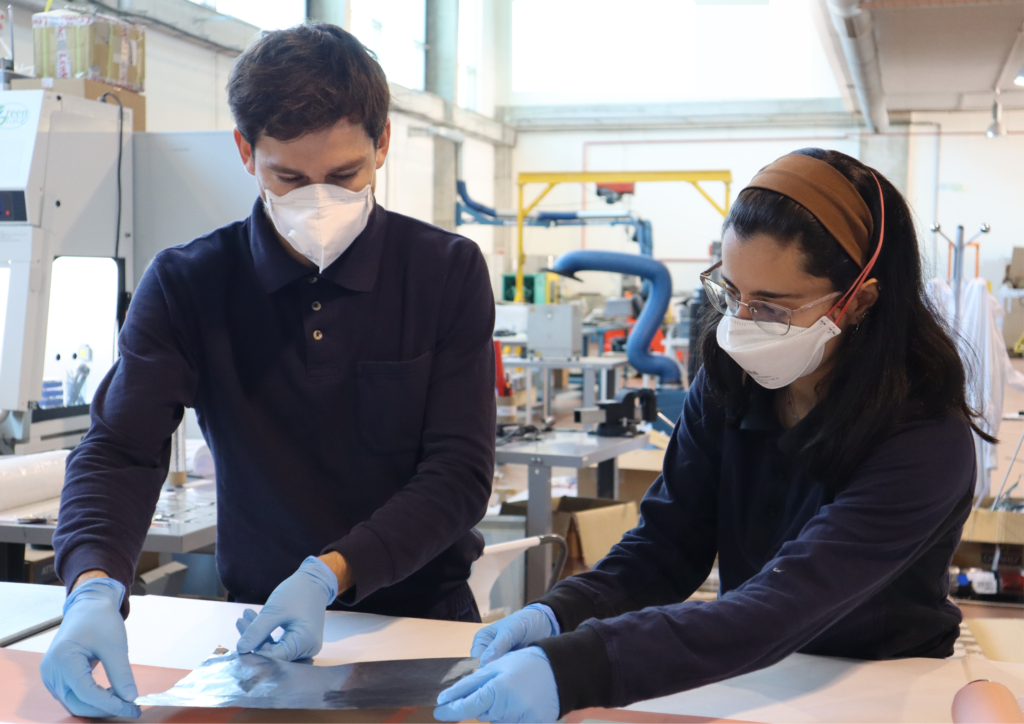
Initially, the joint venture’s business strategy will focus on emerging markets such as EVTOLs (electric vertical take-off and landing vehicles), better known as flying taxis, and drones during the period 2024 – 2026, with a later focus on building a factory with production capacity for electric vehicles.
To accelerate the industrialization of the product, and in recognition of the company’s strong potential, the Center for Technological Development and Innovation (CDTI) recently awarded Floatech a grant through its NEOTEC 2022 program, giving it one of the top 5 ratings among all funded projects.
The competitive commercial process for the manufacture of nanostructured silicon anodes developed by Floatech has the advantage that it does not use mixing processes, solvents or polymers, thus reducing manufacturing costs and CO2 emissions generated.
In addition, the method combines scalability in manufacturing, sustainability and results in the manufacture of LIBs with high performance.
Silicon has ten times the storage capacity of graphite, the most currently used anode material. However, the direct substitution of graphite for silicon has proven to be a relevant technological challenge due to the effects of volumetric expansion that silicon undergoes during charge and discharge cycles.
To preserve this high capacity, the silicon must be nano-sized (< 200 nm) to avoid sputtering after the electrochemical conversion reactions that occur during lithium storage/release.
Floatech has a process to manufacture nanosilicon in a textile format that allows it to be introduced directly into the LIB production line. The company believes that its transformation process is the most scalable currently available.
Floatech’s core technology was developed in a research project of excellence funded by the European Research Council, through the prestigious ERC Starting Grant and ERC Proof of Concept programs, carried out at IMDEA Materials.
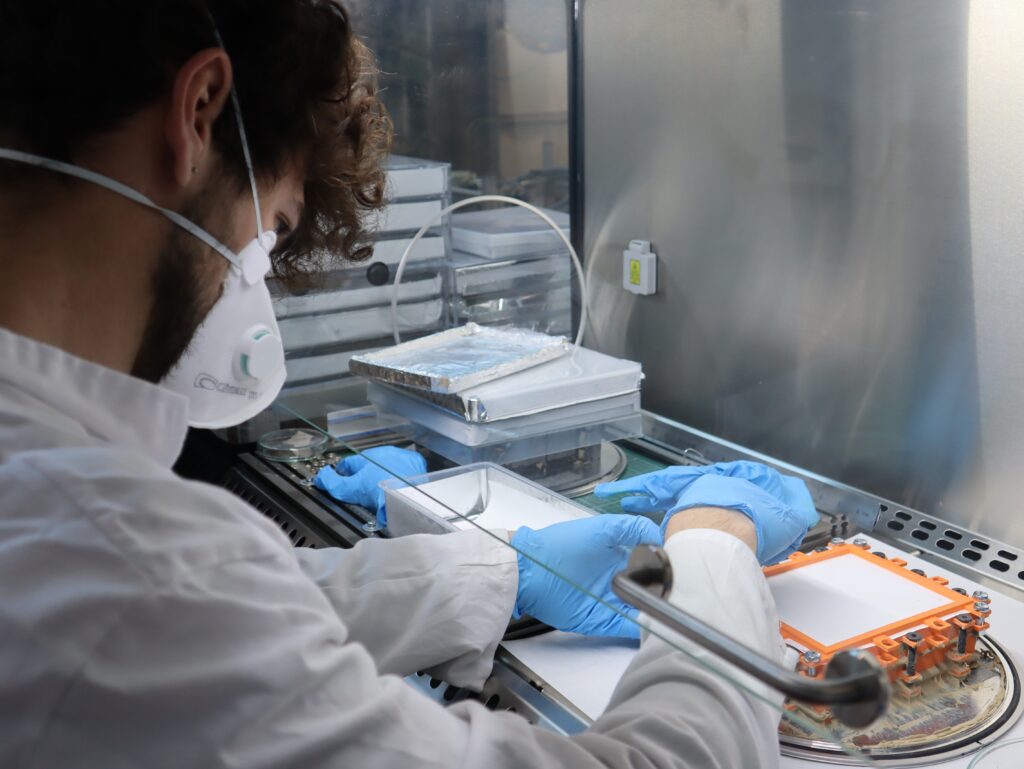