- Metal Organic Frameworks (MOFs) have long been studied for their potential benefits in processes requiring programmable, highly porous materials.
- Now, IMDEA Materials researchers are applying computational techniques to go beyond traditional MOFs via the introduction of polymer composites, improving their mechanical performance and industrial scalability.
A new class of materials could prove significant in more efficient carbon capture technology, drug delivery and even as a gateway to the hydrogen economy.
Metal Organic Frameworks, or MOFs, have been studied for more than three decades. Yet their industrial applicability is still being fully understood by researchers today.
“Since their discovery in the 1990s, MOFs have become highly popular materials due to their interesting properties and wide range of applications including gas separation and storage, drug delivery and fire-safe plastics,” explains IMDEA Materials Institute’s Dr. Phuong Vo.
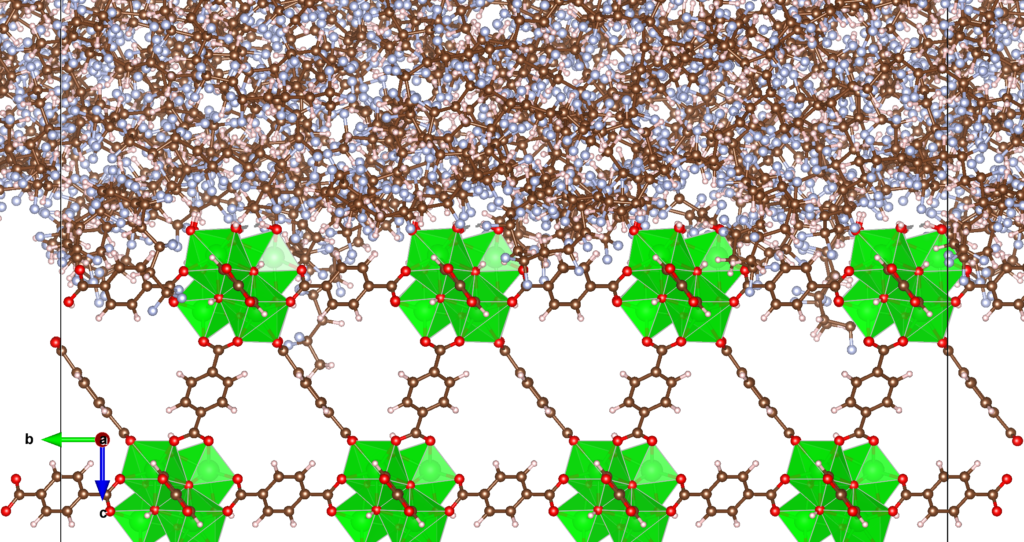
As their name suggests, MOFs are constructed from metal and organic building blocks. Due to their topologies, MOFs have an ultrahigh porosity, exceptional internal surface areas and structural tunability which make them highly suitable for various gas separation applications.
Functioning as a kind of high-tech sponge, these materials can be fine-tuned to separate and trap harmful CO2 emissions released during the industrial process before they reach the atmosphere.
This is an area of high importance, in particular to the oil and gas industry. Gas separation using membranes is considered a highly attractive, energy efficient technique for CO2 capture.
MOFs’ potential for hydrogen (H2) storage is also still being explored. H2 is seen by many as one of the most promising alternatives to traditional fossil fuels to minimise carbon emissions.
However, even though H2, as a fuel, has the highest energy content per unit of mass (energy density per unit of mass), it has a low energy density per unit of volume. This low density at room temperature complicates its storage, as it requires more space than other fuels unless it is compressed or liquefied.
Enter MOFs, the ideal materials for H2 storage based on physisorption, the process whereby gas molecules are physically bonded to the surface of a solid or liquid that the gas comes into contact with at low temperatures.
Having been pioneered more than 30 years ago, however, researchers are now looking to go beyond typical MOF materials, either by improving their mechanical properties, and/or by making them more industrially scalable.
“MOFs face several limitations in terms of mechanical flexibility and film formation,” says Dr. Vo. “To address this issue, scientists are now combining them with polymers to create a new type of materials known as Metal Organic Framework Mixed Matrix Materials, or M4s.”
“As with all composite materials, the objective of adding polymers to existing MOFs is to achieve greater properties than those found in the individual components.”
“For example, while MOFs offer excellent porosity and large internal surface areas, they can suffer from limited stability. By adding polymer materials, we can enhance this stability, while retaining their beneficial characteristics.”
Dr. Vo is a postdoctoral fellow, financed by the European programme Marie Skłodowska–Curie Actions, working in IMDEA Materials’ Computational and Data-Driven Materials Discovery research group, led by Dr. Maciej Haranczyk.
Her research is being carried out as part of the M4MID project, which aims to develop a high throughput computational method for creating M4s with the optimum mechanical properties.
While adding polymers to existing MOFs can enhance their performance, this is ultimately determined by how those individual components interact at the nano level.
By employing machine learning techniques, researchers will be able to predict the exact properties of these interfaces within M4 materials.
“Within M4MID we have three main objectives,” explains Dr. Vo. “First, we will develop a multiscale computational workflow to predict mechanical properties of M4s from the atomic to the micro scale and then verify these predictions through experimental testing.”
“After that, we will perform these processes in a high-throughput simulation to generate datasets which will be used to fulfil our final objective: to build machine learning models to computationally design M4s with good mechanical properties.”
M4MID, which kicked off in June, 2023, is a two-year project due to wrap up in 2025.
The “Toward Desirable Metal Organic Framework Mixed Matrix Materials through Machine learning-guided Interface Design” project has received funding from the European Union’s Horizon MSCA Postdoctoral Fellowships programme 2021 under the grant agreement 101067497.
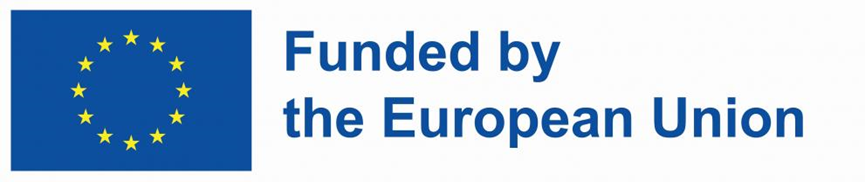