Researchers at IMDEA Materials Institute now have access to a powerful new tool to characterise, design and create novel materials with a wide range of applications, including next-generation biomedical devices.
IMDEA Materials recently became just the third scientific research institute in Spain, and the only one in the Madrid region, to operate an advanced SAXS/WAXS laboratory beamline with synchrotron detector technology.
The advanced piece of equipment, made to measure in Austria for IMDEA Materials’ specific requirements, was purchased through the Institute’s role in the Community of Madrid’s MAMAP-CM project.
MAMAP, or Materials and Models Against Pandemics, was launched in 2021 to leverage IMDEA Materials Institute’s expertise in materials design and development, device manufacturing, and modelling and simulation – to protect, fight and forecast pandemics.
A key element of the project has been the development of a new generation of biomedical materials and devices, primarily through the Institute’s Biomaterials and Regenerative Medicine and Bio/Chemo/Mechanics of Materials research groups, led by Dr. Jennifer Patterson and Prof. Javier LLorca.
Acquisition of the SAXS/WAXS laboratory beamline technology will allow IMDEA Materials’ researchers to advance this work while also contributing to many of the Institute’s other research areas.
One of the capabilities of SAXS/WAXS that makes it so attractive is that it permits real-time, in-situ measurements. This offers greater opportunities to conduct a wider variety of materials testing and characterisation such as thermoanalysis.
“These kinds of capabilities mean that researchers can study how variable factors such as heat and tensile stress affect the internal structure of materials over a prolonged period,” explains Dr. Juan Pedro Fernández.
“This ability is particularly relevant in the biomaterials field, as researchers need to be able to simulate the real-world conditions that these materials will face, and understand how their properties will evolve during use.
“How materials will react to temperature changes, or to coming into contact with organic fluids with different pH, to constant stresses etc. This knowledge is essential in being able to design and improve biomedical devices.”
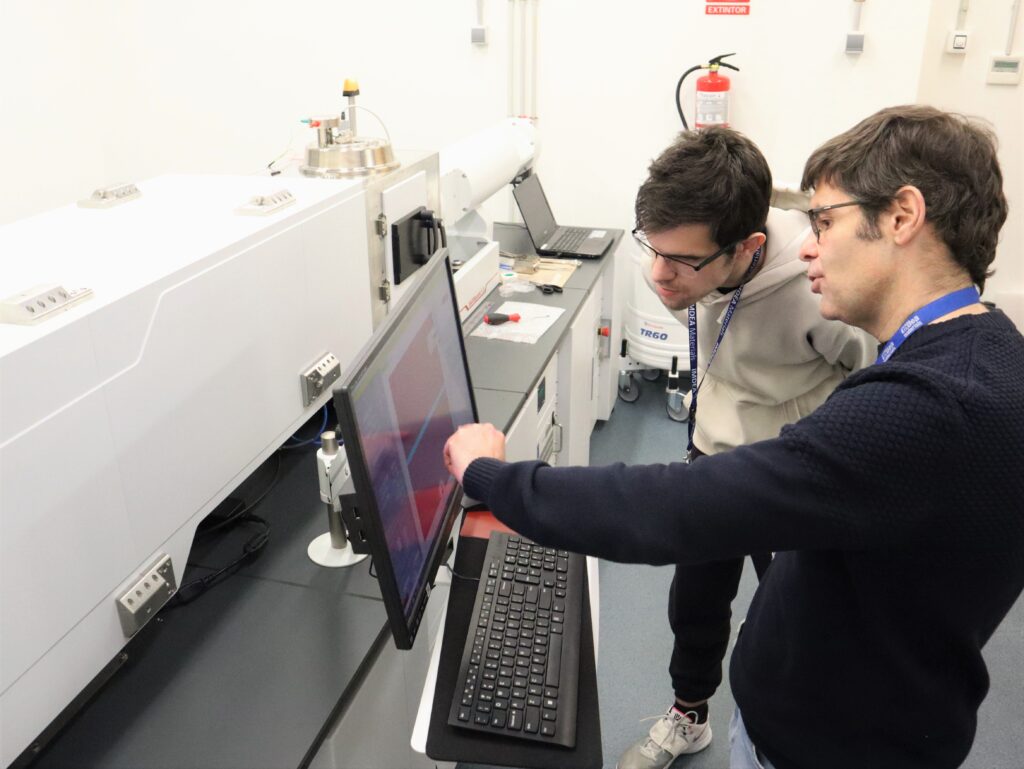
The institute’s SAXS/WAXS technology also has applications in a variety of other fields from battery testing to creating shape-morphing flame-retardants for use in polymer composites.
SAXS/WAXS has the capabilities to allow researchers to study the internal properties of materials down to the atomic level, while also permitting real-time, in-situ thermal, tensile or electrochemical measurements.
SAXS, or Small-Angle X-ray Scattering and WAXS, or Wide-Angle X-ray Scattering, are complementary characterisation techniques through which researchers can peer inside materials to their most basic level.
This is done through the use of a focused X-ray beam, which is targeted at a sample of the material that researchers wish to study.
In the case of WAXS, researchers are then able to measure the spaces between individual atoms. Such calculations are carried out using angstroms, a unit of measurement equal to 0.0000000001 of a metre.
“When the X-ray beam comes into contact with this sample, these X-rays can be diffracted,” explains Dr. Juan Pedro Fernández, senior postdoctoral researcher at IMDEA Materials. “This occurs if the X-ray wavelength is similar to the inter-atomic spacing in the crystals, which then creates a WAXS pattern.”
“However, depending on the electronic densities, the beam can also be scattered by the particulate matter of solid, liquid or gaseous nanostructures. This leaves a SAXS pattern.”
“These patterns are captured by the machine. By analyzing them, we can discern information relating to the interior nature of the material that we are studying in a non-destructive way.”
Where SAXS/WAXS comes into play is in offering researchers the ability to study this scattering at both very small angles, typically 0.1-1° and at much wider angles greater than 2°.
Being able to analyse scattering at different angles means a greater range of information can be obtained. While SAXS is typically used to analyse nanostructures on a larger scale, WAXS can observe details at the atomic level (crystalline structures) that cannot be measured using only short-angle scattering.
“This type of capacity gives us the ability to understand much more about the structure of the materials that we are dealing with,” says Dr. Fernández. “If you can’t understand a material and its behaviour, there’s no way that you can work to improve its properties, which is the basis of what we are trying to do here at IMDEA Materials.”
Importantly, the new technology also offers much faster acquisition time than other X-ray diffraction laboratory technology. While common diffractometers require up to 20-25 minutes to achieve a good WAXS analysis, the laboratory beamline can arrive at a similar result in just seconds.
Another capability of SAXS/WAXS that makes it so attractive is that it permits real-time, in-situ measurements. This means that researchers can study how variable factors such as heat and tensile stress affect the internal structure of materials over a prolonged period.
“This research is funded through the project “MAMAP-CM – Materials and models against pandemics” (REACT-EU resources of the Madrid Operational Program 2014-2020, in the action line of R+D+i projects in response to COVID 19). Project funded by the Community of Madrid and by the ERDF “A way of doing Europe”. Funded as part of the Union’s response to the COVID-19 pandemic, through the agreement signed between the Community of Madrid and the IMDEA Materials Foundation to carry out actions in research on SARS-COV 2 and COVID-19 disease financed with ERDF REACT-EU resources.”
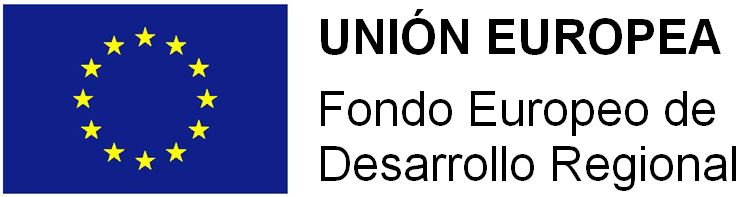