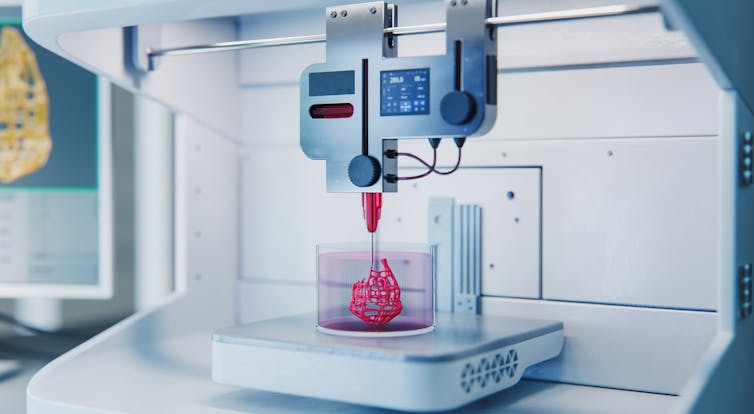
Mónica Echeverry Rendon, IMDEA MATERIALS
Shoulder joints, knee prostheses, cardiovascular stents, not to mention dental prostheses, facial implants, breast implants in cosmetic surgery, discs to replace vertebrae, damaged or non-functional tissues replaced by new ones. The list of possible “replacements” when something goes wrong is growing longer every day.
Until now, implants have been standardised. Patients must adapt to pre-set sizes and dimensions. This is the main reason why, for example, a knee prosthesis wears out prematurely or requires months of rehabilitation – the body must adjust to the implant. However, we are advancing in the development of processes and materials that allow for the opposite: each patient receiving an implant custom-made to fit their body.
The Moment of Surgery
Various medical fields use implants with pre-designed shapes and sizes, which are adjusted to the patient’s needs – often chosen at the time of surgery itself.
Clear examples include shoulder, knee, or hip joint replacements. Orthopedic surgeons select from different sizes and types of prostheses during the procedure, depending on what best suits the anatomy and condition of the bone.
A similar situation occurs during the implantation of cardiovascular stents. Specialists have sets of implants available and decide on the best one based on what they encounter during surgery. The same process is repeated in other fields, such as dentistry and even plastic surgery.
We Are Not All the Same
Each individual has unique anatomical and physiological characteristics. No one has the exact same knee as someone else, just as no two people have identical eyes. Additionally, factors such as age, ethnicity, and the patient’s medical condition at the time of needing the implant significantly affect the ideal characteristics of the best possible implant.
The goal is to meet specific needs so that patient recovery is faster and more effective. In other words, if we were talking about clothing sizes, we shouldn’t just have S, M, L, and XL—we should be able to find a perfectly tailored fit. Thinking about “custom-made implants” brings us closer to achieving this goal.
How to Get a Custom-Made Implant
The fields of biomaterials, tissue engineering, and medical imaging are currently at the forefront of research for developing and designing implants that meet patient needs. To create a “menu” of implant options, several key ingredients must be developed:
As a starter, the acquisition and processing of medical images must be considered. X-rays, MRIs, and CT scans provide highly precise anatomical and functional details. These technologies reveal what each patient will need and allow for the design of implants based on the size, shape, and location of the issue. They also help evaluate the patient’s medical condition. Mathematical modeling and computer-assisted personalized simulations predict behaviours and assist in selecting the best option.
However, the main course of a custom-made implant is material selection – a powerful tool in medical implantology.
The Revolution of Shapes
The materials used today for implants and prostheses can be either permanent or degradable. In terms of composition, they can be metallic, ceramic, polymeric, or combinations of these. The best materials are selected based on the mechanical and biological characteristics of the tissue being replaced.
The same material won’t be used to replace hard tissue like bone versus a more flexible tissue like skin. When selecting compatible materials, allergies and intolerances must also be considered to ensure a good foundation for tissue restoration.
Then comes the dessert: the manufacturing of the implant. Achieving various shapes, geometries, and configurations is crucial, and the manufacturing technique used plays a critical role in fine-tuning the implant’s performance.
There are numerous options, from dense solid pieces to porous or gradient structures: three-dimensional scaffolds, thin films, fibres of different dimensions, and more.
Shape-Memory Materials
Both traditional techniques (machining and forming) and advanced techniques such as additive manufacturing (3D printing) are used to create implants.
Taking it a step further, we can develop 4D materials. Thanks to this innovative technology, implants can change their shape, properties, and function in a controlled manner over time. For example, some materials can be folded inside syringes and injected directly at the defect site.
This approach can be further enhanced with special coatings that help the body interact better with the implant by modifying surfaces or adding molecules.
Tissue Regeneration
At the IMDEA Materials Institute, we are working on developing copolymers for tissue regeneration – structures that replace or reinforce damaged tissues to help restore their function. These materials are highly useful for skin grafts, articular cartilage repair, and even bone implants.
The material we have developed can be printed using a 3D bioprinter. We can customise its composition, combining different compounds and configurations to give it distinct mechanical properties. This means that the same material, with slight modifications, can be used to regenerate skin, cartilage, and bone. Additionally, it is biocompatible and biodegradable, meaning the human body will not reject it.
Many of these advancements are driving a true revolution in implantology. More and better options will continue to emerge, creating a menu tailored to each patient – reducing pain and recovery time.
Mónica Echeverry Rendon, Junior Investigador, BCD Group, IMDEA MATERIALS
This article was originally published in The Conversation. Read the original (original content in Spanish).