- More than four million bone graft and bone replacement procedures are performed each year globally. This number is expected to increase dramatically over coming decades as life expectancies rise.
- IMDEA Materials Institute researchers are working to accelerate the development of post-processing implant heat treatments, creating more durable bone replacements, reducing surgical interventions, and improving patient quality of life.
Researchers at IMDEA Materials Institute are working to ensure that future bone replacement implants are more durable and offer a greater service life than ever before.
The research, which is being undertaken through the European Union-funded M3TiAM project, is designed to meet the needs of an ageing population, with the demand for bone replacement procedures expected to soar in the coming years.
IMDEA Materials’ work on the project involves developing innovative computational tools to predict the effect of post-processing heat treatments on novel, 3D-printed titanium (Ti) alloy implants.
In recent years, additive manufacturing (or 3D printing) has emerged as one of the most promising technologies in bone replacement implant manufacture, as it offers the ability to personalise implants to the needs of the individual patient.
This affords several benefits, in particular by addressing what is known as ‘stress shielding’, a common problem caused by traditional metallic bone replacements and which results in shear stress between bone and implant.
This leads to a reduction in the density, strength and stiffness of the bones around the implant, and a subsequent decrease in patient health and wellbeing. 3D-printed implants can also more closely match bone geometry and improve bone growth within the implant.
“Today, the idea of designing and manufacturing implants via additive manufacturing is nothing new, it’s a technique that everyone is trying to take advantage of,” IMDEA Materials’ Dr. Adrian Boccardo explains.
The relative novelty of the technology however, (the first successful 3D-printed hip prosthesis replacement surgery was only undertaken in April of this year) means that 3D-printed implants present their own limitations.
“What we’ve seen with current 3D printing technology, particularly with selective laser melting (SLM), is that the microstructures of the produced parts are, in many cases, highly fragile,” continues Dr. Boccardo.
“The material will commonly suffer from microdefects that affect it at the atomic level. One of the most prevalent of these is high levels of microporosity, which reduces the fatigue life of the implant.”
“Over time, these defects will affect the functionality of the part to the point where it needs to be replaced surgically, a highly invasive procedure that can cause additional health problems.”
Dr. Boccardo is the lead researcher on the M3TiAM project and a Marie-Skłodowska Curie Actions Postdoctoral Fellow. He is a member of IMDEA Materials Institute’s Modelling and Simulation of Materials Processing research group, led by Dr. Damien Tourret.
One of the most promising avenues to mitigate these microdefects is through the implementation of improved post-processing heat treatments.
Such treatments allow researchers to fine-tune metallic alloys and are commonly applied to 3D-printed parts to improve their mechanical properties, in the case of M3TiAM by reducing porosity.
The computational models to simulate the effects of heat treatment options being developed by Dr. Boccardo will lead to a reduced reliance on costly experimental trial-and-error approaches.
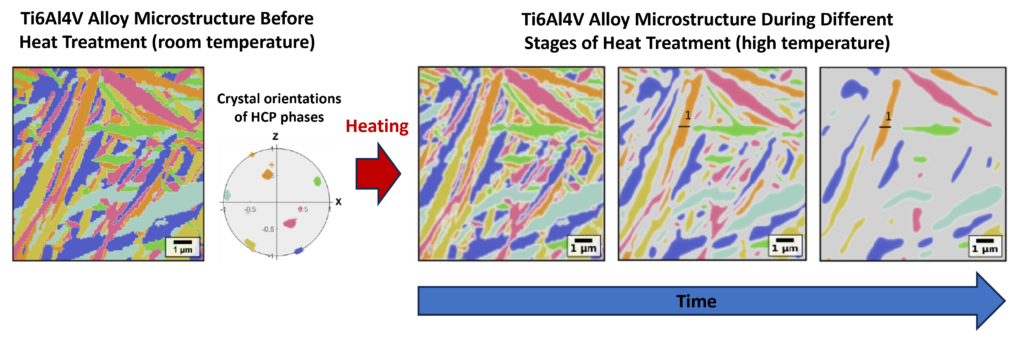
This, in turn, will result in implants which are designed and manufactured faster, at lower cost, ultimately making them both more affordable and accessible for patients. That is of particular importance to the health care industry given the growing demand for bone implants, in particular hip and knee replacements.
Longer life expectancies have resulted in patients increasingly outliving the service life of their original implant, necessitating a secondary surgical intervention to replace it.
In the United States alone, more than 635,000 hip replacements and 72,000 hip revision surgeries per year are expected by 2030. Bone fracture near the implant site, implant wear, fatigue, fracture and loosening are all factors that negatively affect the health outcomes of implant recipients.
Of those undergoing a hip replacement, 5% will require revisional surgery within 10 years, increasing to 15% within 20 years, representing potentially thousands of avoidable surgical interventions each year.
In Spain, there are currently around 35,000 hip replacement surgeries alone annually.
Any new additive manufacturing processes to come from M3TiAM will face both a lengthy regulatory approval process, and the typically winding path to industrial adoption.
Yet Dr. Boccardo remains hopeful that patients would start to see the real-world impact of the improved implant technology within the next 5-10 years.
“Ultimately I am optimistic because the additive manufacturing techniques that we are dealing with are now quite commonplace,” he said. “At the same time, the computational techniques that we are using are also quite standard. So, we’re not reinventing the wheel here.”
“The challenge here is putting these two established technologies together in a way that hasn’t been done before, and where we can achieve the best results.”
The “Multiscale-Multiphysics Modelling of Ti alloy medical implants based on Additive Manufacturing technology (M3TiAM)” project has received funding from the European Union’s Horizon Europe research and innovation programme under the Marie Skłodowska-Curie grant agreement No 101063099. Views and opinions expressed are however those of the author(s) only and do not necessarily reflect those of the European Union or the European Union executive agency. Neither the European Union can be held responsible for them.
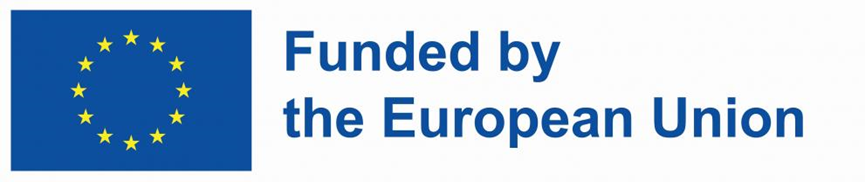