• The European DOMMINIO project has concluded with significant advances in the development of cutting-edge sensors and digital twins.
• Now, IMDEA Materials is preparing for the launch of the COMPSTLAR project: the next step in the use of advanced composite materials in the aerospace industry.
IMDEA Materials will continue its research into improving structural health monitoring processes in the aerospace sector following the completion of DOMMINIO.
Over the past four years of this European project, IMDEA Materials has played a key role in developing a new generation of sensors based on carbon nanotubes (CNTs).
The Institute has also worked on the technology necessary to implement digital twins that allow for real-time damage detection and analysis in aerospace components.
Earlier this year, DOMMINIO held its Final Workshop as part of the 14th International Conference of the European Aeronautics Science Network (EASN).
At this event, researchers from all project partners, including Dr. Davide Mocerino from IMDEA Materials, presented their advances in the design, manufacturing, and monitoring of composite materials for aerospace applications.
The Institute’s research focus has been on the development of advanced sensors and digital twins.
“An important achievement we have made is the ability to objectify the use of sensors,” explained Prof. Carlos González, leader of the Structural Composites Research Group at IMDEA Materials.
“This refers to the process of identifying, characterizing, and selecting specific materials that can be used in the design and manufacturing, in this case, of sensors,” he added.
This process involves evaluating and quantifying the physical, chemical, and electrical properties of materials to determine their suitability for specific sensing applications.
In the case of DOMMINIO, these sensors were manufactured using CNTs, which presents an innovative challenge in the field of aerospace sensors. It is expected that the nanotubes will enable the production of lighter and more sensitive sensors than traditional materials.
“In the world of sensors, one thing is a sensitive material, a material that reacts, and another is a material that always measures the same under the same conditions, with reliability,” commented Prof. González.
“Imagine, for example, that you have a sensor made from a material that is sensitive to temperature. If you take a reading today and tomorrow, but the ambient temperature changes, you have a problem.”
“So, one of the key achievements of the DOMMINIO project is that we have managed, with a sample material, is to understand how the sensor works. It has not been easy.”
However, to commercialise this technology and take it to an industrial level, there is still work to be done. This is where the new COMPSTLAR project, coordinated by AIMEN Technology Center (also the coordinator of DOMMINIO), comes into play.
This project aims to gather real-time data from strain sensors based on novel laser-induced graphene and fiber optics for structural health monitoring and evaluation.
With these fiber optic sensors, Prof. González and his team at IMDEA Materials will continue developing their digital twin to provide real-time simulation of damaged components.
The use of a well-established technology like fiber optic sensors will allow researchers to move more quickly with the digital twin, which relies on the accuracy of sensor data for its development.
“If an impact occurs at a specific point, causing damage,” explains Prof. González, “to repair it, the damaged material needs to be removed and a new piece placed.”
“The digital twin will allow the structural health of the unrepaired material to be analysed virtually and the necessary repairs to be evaluated, based on the data received from the sensors.”
In this way, researchers hope to optimise the maintenance process and reduce material wear.
Another component of the project will be ultrasonic inspection (UI) of materials for damage detection, specifically aiming to improve the detectability of this technique through the use of artificial intelligence (AI).
This research will be led by the In-Situ Processing and Characterisation of Materials group at IMDEA Materials, headed by Dr. Federico Sket.
“Previous research has demonstrated the suitability of combining UI signals with X-ray tomography (XCT) inspection techniques and AI to enhance ultrasonic inspection detectability,” explained Dr. Sket.
“In COMPSTLAR, our focus is on combining ultrasonic inspection during processing, post-inspection with XCT, multivariate optimisation, and AI-based models to improve the subsurface detectability of defects and address the limitations of existing technology, ultimately contributing to improved manufacturing process control and defect reduction.”
This project has received funding via the European Union’s Horizon 2020 research and innovation programme under the grant agreement n.º 101007022.
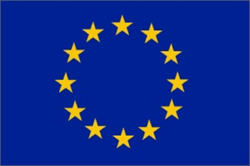