Scientists from the Universidad Carlos III de Madrid (UC3M) and IMDEA Materials Institute have developed a new experimental technique in fragmentation tests to evaluate the energy absorption capacity in the event of impact of metallic structures manufactured using 3D printing.
This technique, which is more flexible, simpler and faster than others currently used, makes it possible to test the mechanical performance of these materials as protective structures.
The main applications of this research are related to the aeronautics, aerospace engineering, security and civil engineering sectors, areas where it is essential to develop new materials to build lightweight, portable protective structures that can be repaired in service and that also have the ability to absorb energy in the event of an impact.
For example, in the event of a collision of a bird with an aircraft, in accidental collisions between motor vehicles or in explosions that may occur in attacks on government buildings and critical infrastructures, such as nuclear power plants, the researchers say.
“The idea is to be able to manufacture protective structures with 3D printing to reduce their cost, minimise waste, personalise their design and offshore their manufacturing, given that it could be carried out in-situ, which would be a great advantage especially for aerospace and defence applications,” explains Juan Carlos Nieto Fuentes, Marie Curie CONEX-Plus researcher (GA 801538) from UC3M’s Department of Continuum Mechanics and Structural Analysis, who recently published this work in the Journal of the Mechanics and Physics of Solids.
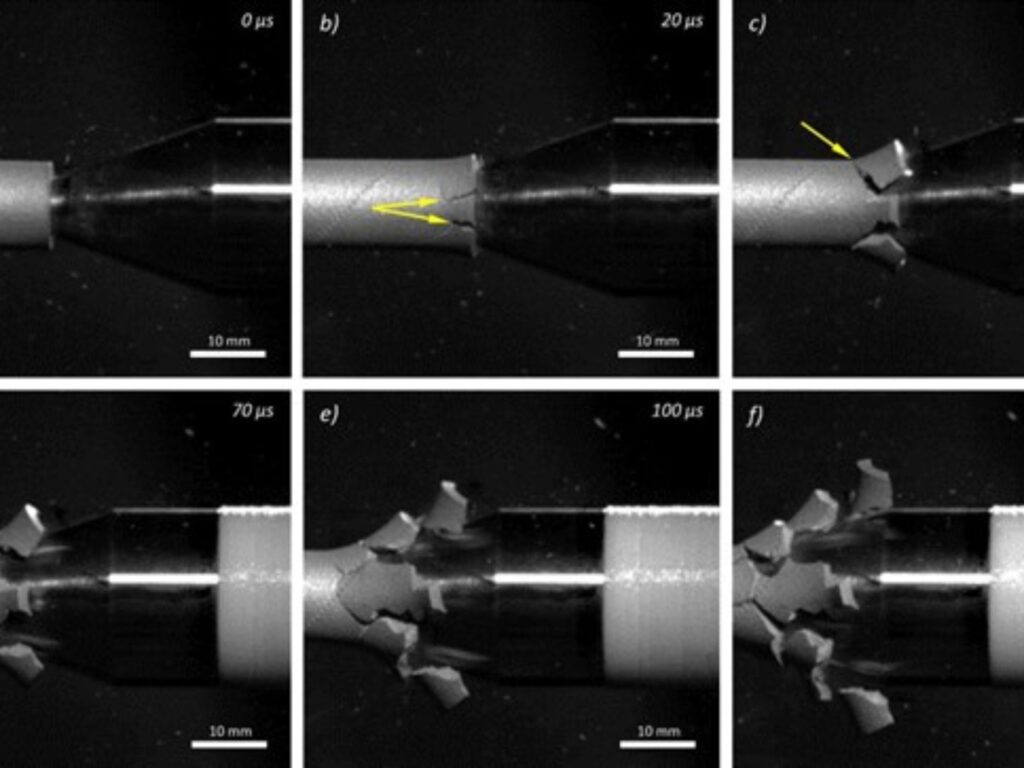
“The article presents a new experimental technique launched at the UC3M Impact Laboratory, where we carry out fragmentation tests at impact speeds of up to 400 metres per second,” explains another of the authors, José Antonio Rodríguez Martínez, a Senior Lecturer in the same UC3M department and a Visiting Reseacher at IMDEA Materials, who has developed this research within the framework of PURPOSE, a European Union ERC Starting Grant (GA 758056) project.
The researchers have filmed these tests with two high-speed cameras and have also carried out X-ray tomography of the printed material structures, before and after being tested, with the collaboration of colleagues from the IMDEA Materiales Institute, who have carried out the microstructural characterisation of the samples.
“Specifically, we have determined the distribution in shape and size of the pores resulting from the printing process and we have investigated their effect on the formation and propagation of cracks, and thus on the energy absorption capacity of the structure,” says Federico Sket, Principal Investigator at IMDEA Materials, who has participated in this study from this research institute together with his colleague Jonathan Espinoza, research assistant at the institute.
The fragmentation experiments were carried out at the UC3M Impact Laboratory using a helium-driven gas gun. Specifically, the researchers launched a circular, conical-nosed projectile weighing about 150 grams that hit a thin-walled tube at speeds ranging from 200 to 400 metres per second (between 720 and 1,440 km/h). In this case, the diameter of the projectile is larger than the diameter of the tube, which expands radially as the projectile advances, until multiple fractures form, resulting in fragmentation of the sample.
“The technique is simpler, faster to use, flexible and has a lower operating cost than systems that use explosives or electromagnetic systems. Our device also allows us to carry out more experiments in less time and thus obtain a number of tests that provide statistically significant results,” explain Sergio Puerta and David Pedroche, laboratory technicians from UC3M’s Department of Continuum Mechanics and Structural Analysis, who were involved in carrying out the experiments.
The researchers say that this is a pioneering methodology and hope to lay the foundations for a protocol that will make it possible to systematically determine whether a printed structure is capable of absorbing energy upon impact, based on the characterisation of its porous microstructure and its correlation with fragmentation mechanisms.
“This technique will ultimately tell us whether metal 3D printing is a viable technique for building protective structures,” says José Antonio Rodríguez Martínez. “In the US there are already specific programmes promoted by the Department of Defence and the Department of Energy to fund this line of research, so we hope that the European Union and the Government of Spain will also develop a long-term vision that will allow us to bring the fundamental research we are carrying out into engineering practice,” he concludes.
Bibliographic reference: J.C. Nieto-Fuentes, J. Espinoza, F. Sket, J.A. Rodríguez-Martínez (2023). High-velocity impact fragmentation of additively-manufactured metallic tubes. Journal of the Mechanics and Physics of Solids, Volume 174, 105248, ISSN 0022-5096, https://doi.org/10.1016/j.jmps.2023.105248