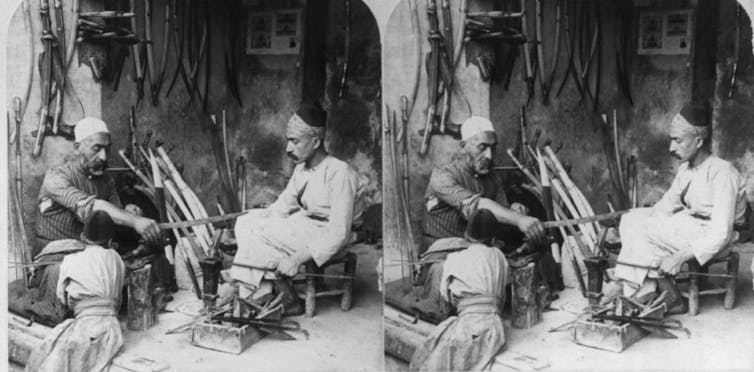
José Manuel Torralba, IMDEA MATERIALES y Ilchat Sabirov, IMDEA MATERIALES
Damascus steel swords were legendary for their great strength, durability and their “almost eternal” edge. They could cut silk as well as shatter a rock. Sultan Saladin impressed Richard the Lionheart at a sword exhibition. The sultan’s blade, slender, light and of an opaque blue typical of Damascus steels, was able to sink into a soft cushion of feathers.
Blacksmiths and metallurgy experts searched for centuries for the secret that made them the most desired weapon of their time. However, it has taken centuries to remaster the technique of manufacturing Damascus steels.
Nowadays, in the world’s most advanced laboratories, we can once more obtain steels that combine that strength and durability by recreating the structure of that mythical material whose forging was attributed by the Christians of the Crusades to Lucifer himself.
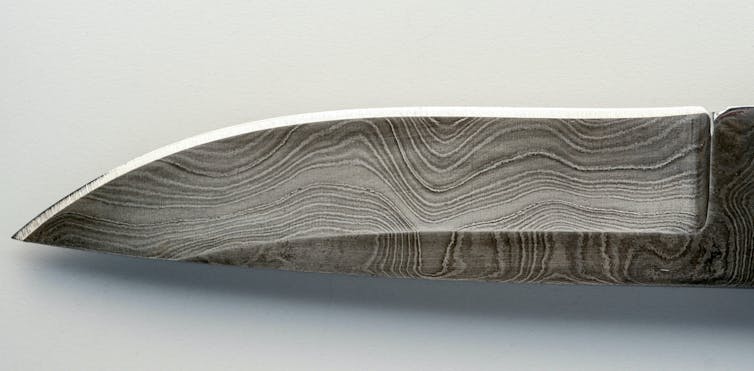
Katanas, Toledo steel and Damascus steel
Like the secret forging processes of Japanese samurai katanas or Spanish Toledo steel, known throughout Europe in the Middle Ages, the production of Damascus steel was passed down from generation to generation of metallurgists for centuries. These techniques, once almost lost for centuries, are now being rediscovered.
A recent scientific publication from the prestigious Max-Planck-Institut für Eisenforschung (MPIE) in Düsseldorf shows that by imitating the manufacturing principles of Damascus steel, the properties of the many modern steels can be matched, or even surpassed, while only using cheap and readily available raw materials.
The secret of its internal structure
Man’s use of iron changed the world. The first iron-based materials, known as wootz steels, appeared in India around 200 BC. These steels were obtained by forging iron sponge mixed with carbon from various natural sources.
At the same time, Chinese metallurgists were developing something similar to cast iron. However, its high carbon content made this material incredibly brittle and therefore largely useless.
Examining Damascus steel, it was discovered that the forging techniques employed created a hierarchy of microstructures in which ductile layers (which can be easily deformed) alternate with hard (more brittle) layers, resulting in mechanical properties far superior to those of other steels. The diffusion processes during their production made the sheets very ductile, allowing changes and transformations, but, at the same time, incredibly tough.
However, for more than 1,000 years, the cost of producing these steels meant that their use was limited to very specific cases where a very sharp edge was needed, such as knives, razors and swords. It was also used to manufacture small and complex parts, such as springs for watches.
It was not until the end of the 19th century, with the invention of modern steel production techniques, such as the Bessemer process, mankind was able to produce steels as the structural material we know today.
The modern steel production process
The 21st century has so far brought a number of advances in this field. We can take, as two examples, 3D printing and new heat treatments such as quenching and partitioning (Q&P), two production methods currently being studied at IMDEA Materials Institute.
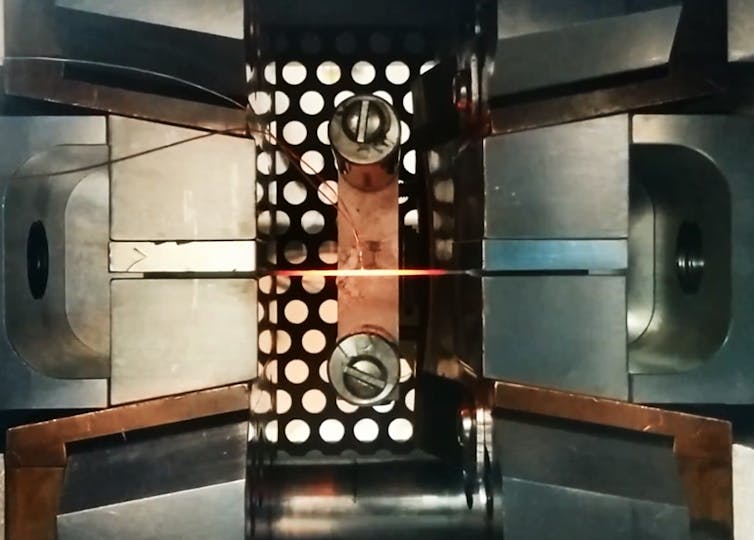
The main objective of the current research is to generate microstructures in steel sheets that not only exhibit improved mechanical properties, but also application-related properties such as fatigue, fracture and impact resistance, together with formability and weldability.
Recently, IMDEA Materials has also started active research in the area of 3D printing of carbon steels for structural applications. The focus is on processing parts with a set of diverse properties suitable for the final application of complex shaped steel parts.
Learning from the lessons of the past
Although this type of research is at the forefront of steelmaking today, in some ways we are still playing catch-up with the metallurgists of the past. In the MPIE publication cited above, metallurgists were able to reproduce the hierarchical structural fabrication process of thousands of years ago, alternating ductile and hard layers. The researchers succeeded in producing a steel capable of withstanding 2000 MPa, but with a deformation of 25 %, far higher than any modern technique.
To put this achievement in perspective, the strongest steels (known as maraging steels) currently used in the aerospace industry can reach 2 500-2600 MPa, but with the drawback of having a poor level of deformation (4-5 %).
This level is much lower than that achieved using the Damascus steel process and results in a strong but brittle material that can break under stress or impact. Meanwhile, steels produced by Q&P have shown an improved ductility of around 14%, but at the expense of the strength shown by maraging steels, reaching around 1 500-1 600 MPa.
In another recent paper published in Nature by MPIE scientists, also based on the development of a hierarchical microstructure like that of Damascus swords, even better results are obtained. But the latter publication takes advantage of rarer and costlier alloying elements, as well as modern technology such as state-of-the-art 3D printing technology.
However, the real achievement of MPIE’s research is the results obtained by relying solely on non-critical alloying elements together with conventional forging and heat treatment technologies.
Advanced tools based on artificial intelligence and machine learning will gradually replace the trial-and-error approach to steel development and fabrication. But, at all times, let the arrogance of progress not prevent us from seeing the genius of those who came before us and all that they have to teach us.
José Manuel Torralba, Professor at Madrid’s Universidad Carlos III University and Director of IMDEA MATERIALS and Ilchat Sabirov, Senior Researcher, IMDEA MATERIALES
The article was originally published in The Conversation. Read the original (content in Spanish).