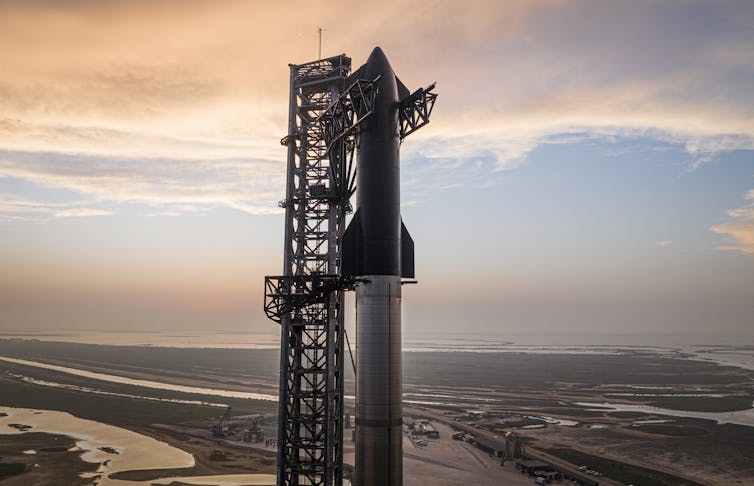
José Manuel Torralba, IMDEA MATERIALES
In a recent recorded conversation between Adam Burrows, an astrophysics professor at Princeton, and Elon Musk, Burrows expressed surprise at SpaceX’s choice to use stainless steel for the Starship spacecraft.
Instead of opting for more “aerospace” materials like carbon fibre composites or aluminum-lithium alloys, Musk’s innovative private space industry has turned to the tried-and-true stainless steel, the same material used to make kitchen cookware.
This conversation, shared on social media platform X, has gone viral, amassing over 25 million views at the time of this writing.
Musk’s rationale for using stainless steel in the Starship’s oxygen tanks is anything but trivial. The familiar material, which was already seen as advanced technology in early 20th-century buildings like the Chrysler Building in New York, may outperform modern carbon fibre or the well-known aerospace aluminum.
The stainless steel used in SpaceX’s Starship is proprietary and patented but bears a strong resemblance to conventional household stainless steels.
Starship: A Revolutionary Design
When Musk and SpaceX entered the space race, their engineers examined NASA’s developments in the Space Shuttle program, focusing on what went wrong and what unnecessarily increased production costs. The emphasis was, as it often is, on the choice of materials.
Starship is designed as a cylindrical rocket and spacecraft combination, intended to be a fully reusable transportation system for crew and cargo to low Earth orbit, the Moon, or Mars. It is arguably the most powerful launch vehicle ever developed, capable of carrying up to 150 metric tons in a fully reusable configuration and 250 metric tons in expendable form.
The Distinctive Stainless Steel Hull
Unlike NASA’s shuttle, which resembles an aircraft and requires external fuel tanks, Starship appears as a single rocket. This design allows for better optimisation, particularly of the thermal shield, which has been the cause of several accidents, including the Columbia disaster.
One of the most striking features of the Starship is its shiny stainless steel exterior. But why choose stainless steel, an alloy significantly heavier than carbon fibre or the extremely lightweight aluminum-lithium alloys used in the Falcon 9?
While carbon fibre composites are lightweight and strong, they require fabrication in autoclaves—pressure vessels using numerous layers of woven material (between 60 and 200). Once cured, these surfaces must be modified and painted to ensure a leak-proof seal, a challenging process.
Considering Starship’s nine-meter diameter, creating it from fibre composites would require enormous autoclaves, complicating the technology involved.
Conversely, stainless steel can be cold-formed, ensuring zero microstructural defects. It is also relatively easy to weld and can be polished to a shiny finish, eliminating the need for paint. Although aluminum might compete with steel on ease of manufacturing, it is not as easy to weld.
Withstanding Cryogenic Temperatures
Rocket oxygen tank materials must endure pressurised gases at cryogenic temperatures—below -150 °C—without leaking, something only stainless steel can guarantee.
Furthermore, carbon fibre and aluminum become brittle at such low temperatures, while austenitic stainless steel performs well from these low temperatures up to the extreme heat generated during re-entry, a time when carbon fibre and aluminum struggle despite thermal shielding. Aluminum risks melting, and composites can degrade, while stainless steel remains unaffected.
In terms of weight, it’s true that stainless steel quadruples the density of carbon fiber composites and triples that of aluminum-lithium. However, its strength-to-weight ratio means that the same performance can be achieved with thinner sections, making the total weight competitive with other materials.
In conclusion, old faithful stainless steel emerges as more reliable, leak-proof, competitive in weight and strength, and unrivaled at the pressures and temperatures of space travel. Additionally, manufacturing stainless steel is straightforward and cost-effective.
Cost of Materials
The cost of manufacturing one kilogram of carbon fibre composites is approximately €118/kg. For aluminum-lithium alloys, it’s about €36/kg. In contrast, a kilogram of series 300 (austenitic) stainless steel costs around €3.6/kg.
But is this a special steel that will carry humans into space?
In his conversation with Burrows, Musk explained that they initially experimented with standard market-grade series 300 steels, including austenitic grades like 301 and 304 (the most widely used stainless steel). Eventually, they added a “small tweak” that raises the cost slightly above €3.6/kg, which they patented as 30x steel (also used in Tesla vehicles).
Musk’s approach is reminiscent of chefs adding a “special ingredient” to enhance flavor without fundamentally altering the dish—an innovative touch to the material for patenting purposes.
While carbon fibre and aluminum-lithium are favored in the innovative aerospace industry, stainless steel, commonly used in railings, buildings, sports stadiums, and mechanical components, proves to be effective, economical, and aesthetically pleasing for spacecraft that will take humans far above our planet.
In advanced engineering, a well-selected common material can perform exceptionally well. Complexity does not always equate to superiority.
José Manuel Torralba, Full Professor at the Carlos III University of Madrid, IMDEA MATERIALES
This article was originally published in The Conversation. Read the original (content in Spanish).