- As a member of the HIPped Ultrafan IPT Casing (HUC) project, led by Spanish engine and turbine manufacturer ITP Aero, IMDEA Materials was involved in the development of the UltraFan’s Intermediate Pressure Turbine’s (IPT) casing.
- The UltraFan® demonstrator is the prototype of a future line of engines which are designed to be 25% more efficient than Rolls-Royce’s existing Trent engines. Testing of the Ultrafan demonstrator, which will run on 100% sustainable aviation fuel, will begin later this year.
IMDEA Materials Institute has played an important role in the development of Rolls-Royce’s next-generation UltraFan® engine prototype.
Earlier this year, ITP Aero, one of the world’s largest aircraft engine and turbine manufacturers, delivered the first intermediate pressure turbine (IPT) for the UltraFan demonstrator.
Working as part of the HIPped Ultrafan IPT Casing (HUC) project, IMDEA Materials collaborated on the design and testing of the casing for the UltraFan’s Intermediate Pressure Turbine (IPT).
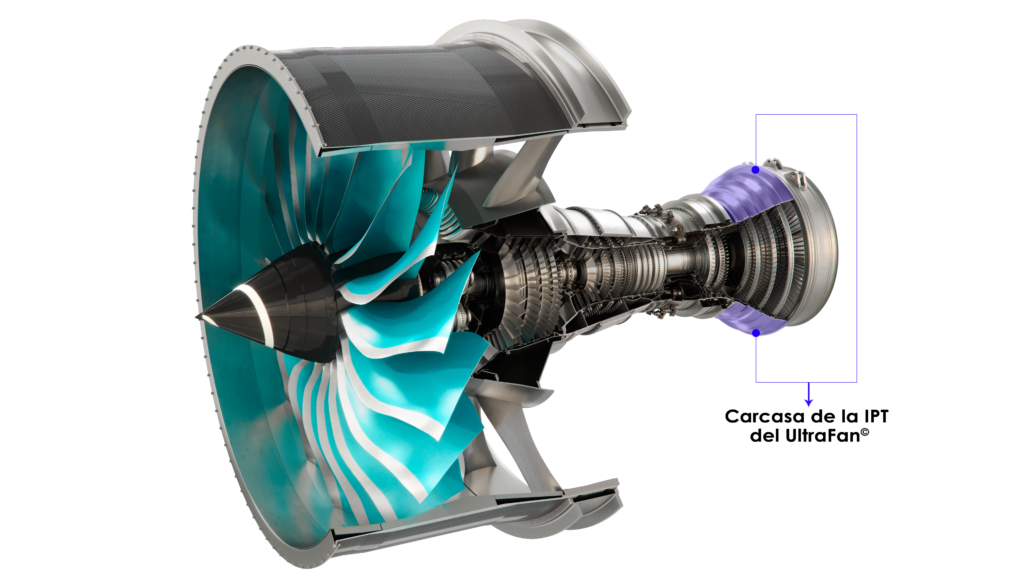
The first tests of the new engine prototype will get underway this year using 100% sustainable aviation fuel.
The casing is the principal static component of the Ultrafan’s IPT; it protects the blades and the rest of the static parts. It also supports load transmission with the rest of the engine.
Additionally, it protects the aircraft by containing the turbine blades in case of failure. The IPT is a key module of the future UltraFan, designed to operate at very high speeds to optimize the engine’s fuel consumption and CO2 emissions.
One of IMDEA Material’s principal researchers in the project, Juan de Pablos Gómez, highlighted how the technology developed through the HUC project will result in considerable benefits for the aviation industry.
“This UltraFan engine is a demonstrator for a series of technologies that will allow the cutting of fuel consumption by 25% and the reduction of noise levels by 35% in the next decades,” explained de Pablos, whose work on HUC was the central component of his recently-completed PhD thesis.
“Other turbofans that will go into operation in the commercial aviation industry will be able to take advantage of these technologies to cut emissions and also to cut costs involved in the manufacture of the engine itself.”
IMDEA Material’s role centred on its Computational Solid Mechanics research group led by Professor Ignacio Romero and its Physical Simulation group led by Dr. Ilchat Sabirov.
“[We] were mainly involved in the computational simulation component, dealing with the mechanical behaviour of this new casing which is made of a new super alloy,” said de Pablos.
“As the UltraFan engine relies on more efficient thermodynamic cycles, it will have to be able to withstand higher temperatures. Our mission, through using new technology developed in computational research, was to be able to assess these mechanical properties of the material before it underwent the required certification process.
“It was also very important for us to understand the behaviour of this material under extreme conditions of strain and strain rate such as when subject to potential blade impact.”
The casing in question houses the turbine blades and connects the IPT to the rest of the engine. As such, it must not only be heat-resistant but also strong enough to contain engine pieces and prevent them from flying loose and hitting the fuselage of the aircraft in the event of internal engine damage.
The groundbreaking nature of the HUC project is based on its innovative use of Near Net Shape powder Hot Isostatic Pressing (HIP) technology and the powdered superalloy Astroloy. According to ITP Aero, Astroloy offers improved mechanical performance at high temperatures compared to more commonly used superalloys.
In the current generation of engines, such casings are typically manufactured from the nickel-based superalloy Inconel 718, a workhorse material used in a variety of components in the aircraft engine industry.
IMDEA Materials was able to bring its expertise in both simulation and experimental research to the project. Along with the Institute’s computational work, Dr. Sabirov’s group also performed a thorough mechanical and microstructural characterisation of the astoloy samples.
“Through this, a wide range of mechanical and application-related properties were studied to ensure the high quality of the final component,” Dr. Sabirov said.
The Madrid-based Institute was one member of an international consortium dedicated to the design and manufacture of the new casing which was coordinated by the Basque Centre for Technical Studies and Research (CEIT) under the management of ITP Aero.
The Italian National Interuniversity Consortium of Materials Science and Technology (INSTM), the Universidad del País Vasco, and powder manufacturer Aubert & Duval SAS were also involved.
The HUC project was jointly funded by the European Union and European aeronautics companies through the Clean Sky 2 programme. The final report of the project was recently approved by the European Commission.
You can read more about the HUC project here: http://huc-cs2.eu/