The project
Triggered by environmental issues, the EU market has a strong interest in development of low-cost and lightweight heavy gauge steels for various applications. The austenitic Fe–Al–Mn–C quaternary alloys have recently been attracting tremendous attention, as they can demonstrate exceptional combination of high strength and high ductility, and do not need expensive strategic alloying elements like Mo, Cr and/or Ni, though they are hard to process materials. The aim of the DELIGHTED project is to gain fundamental understanding of principles of microstructural design for engineering of perspective austenitic lightweight steels to reach the combination of mechanical and performance properties suitable for applications.
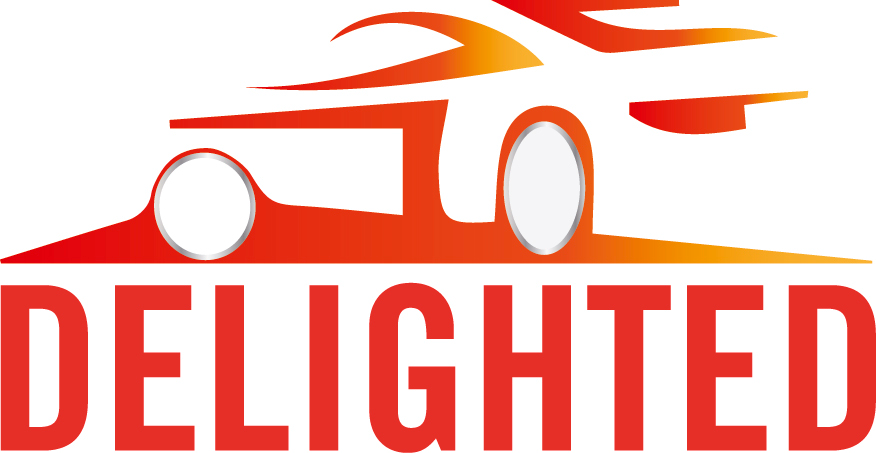
The main objectives of the DELIGHTED project include:
- To understand the effect of the steel chemistry on the microstructure evolution during hot rolling including recrystallization, precipitation and growth of particles and development of crystallographic texture.
- To understand fundamentals of cracking during hot rolling of austenitic lightweight steels, which is necessary for development of novel thermo-mechanical processing routes.
- To describe kinetics of kappa-carbide precipitation and growth in the austenitic matrix with respect to the steel chemistry and heat treatment parameters.
- To establish the relationships between microstructural features of lightweight steels and various technological properties, such as fracture toughness, fatigue resistance, weldability, etc.
- To establish the microstructure – properties relationship in the form of analytical models predicting the mechanical properties of lightweight steels.
- To understand the principles of microstructural design for engineering of lightweight steels exhibiting a combination of enhanced performance properties with improved mechanical strength.
- To design and manufacture a prototype of a cabin for vineyard mini-tractor with the connections made of the developed lightweight steel and to experimentally measure its crash resistance.
News & Events
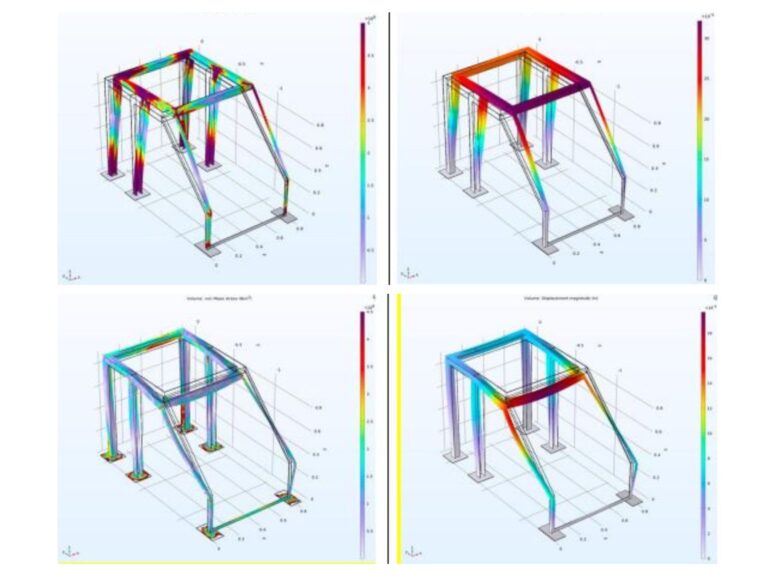
‘Exceptional results’: DELIGHTED praised for delivering significant advances in the production of lightweight, high-strength steel alloys
THE IMDEA Materials-coordinated DELIGHTED project has been praised for delivering “exceptional results” in its successful efforts to develop Advanced High-Strength Steels (AHSS) for lightweight vehicle applications.
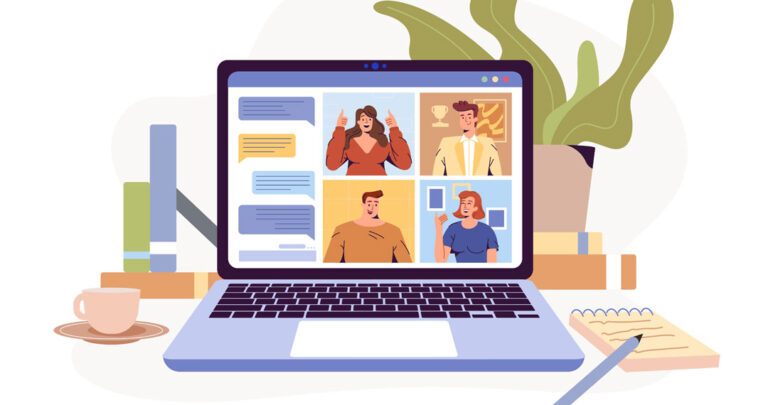
DELIGHTED consortium celebrated final meeting
On February 6, 2024, the DELIGHTED consortium held its final meeting. The partners presented and discussed the latest results from the characterization of the developed steel grades within the framework of the DELIGHTED project.
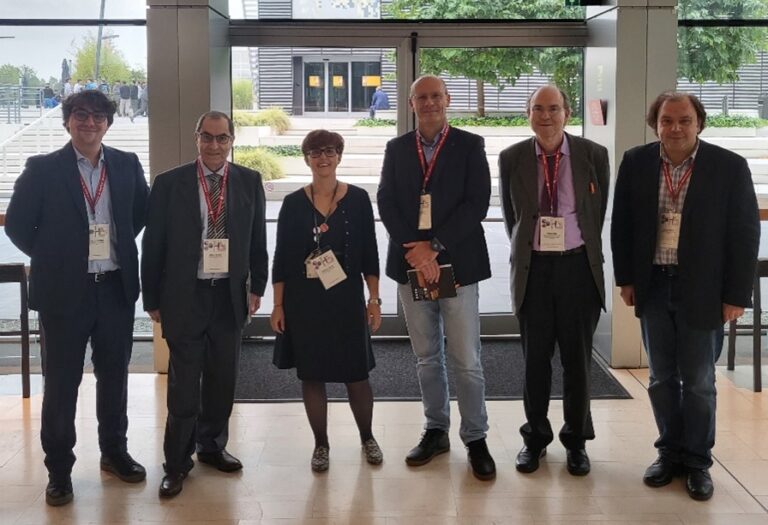
DELIGHTED participates in the International Workshop High Strength Steels – HSS 23
The DELIGHTED consortium members played a significant role in organizing the International Workshop “High Strength Steels – HSS 23”.
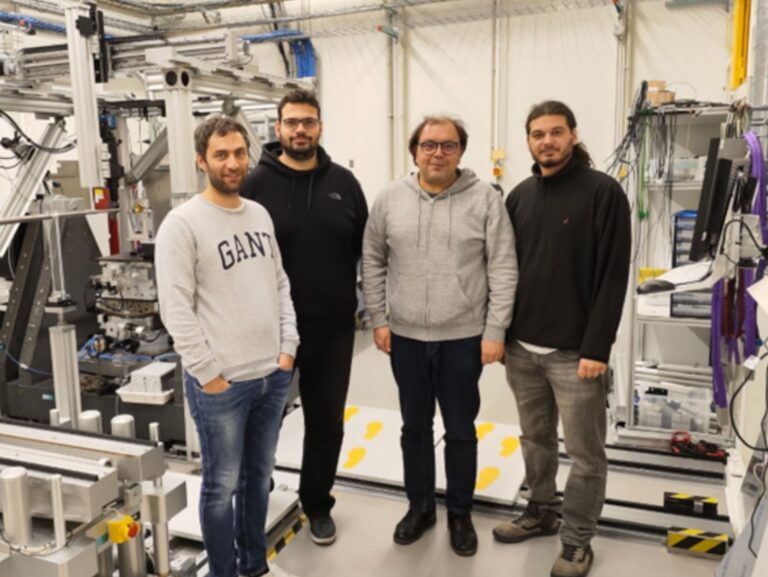
Synchrotron Study Unveils Secrets of K-Carbides in Advanced Steel Alloys
DELIGHTED researchers successfully conducted in situ synchrotron X-ray diffraction studies on a steel grade developed within the project framework at the P21.2 beamline of PETRA III at DESY (Hamburg, Germany) earlier this month (October 2 to 4), 2023.
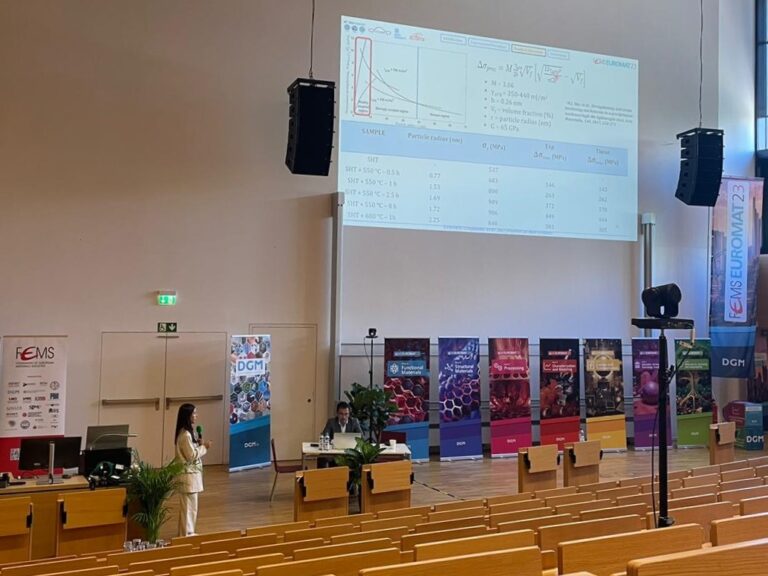
DELIGHTED project’s latest results presented
The DELIGHTED consortium continues to disseminate the project results. Andrea Gómez Fernandez from IMDEA Materiales gave a talk about the effect of aging on microstructure and mechanical properties of Fe-30Mn-9Al-1C steel on macro- and microscales at EUROMAT 2023.
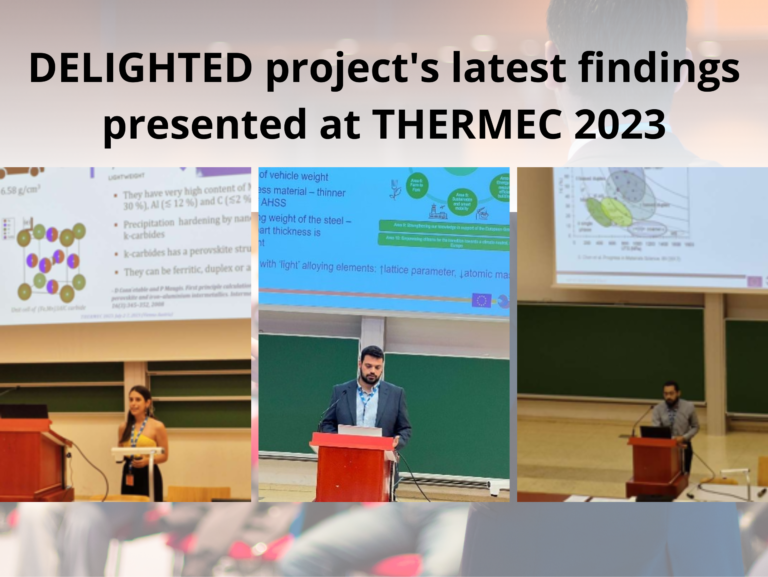
Unveiling Breakthroughs: DELIGHTED Project’s Latest Findings Presented at THERMEC 2023 Conference
The dissemination activities of the outcomes of the DELIGHTED project are ongoing. Researchers from consortium members the Max-Planck Institute for Iron Research, IMDEA Materials Institute and the University of Ghent presented the latest DELIGHTED results at the THERMEC 2023 Conference in Vienna.
Publications
Partners
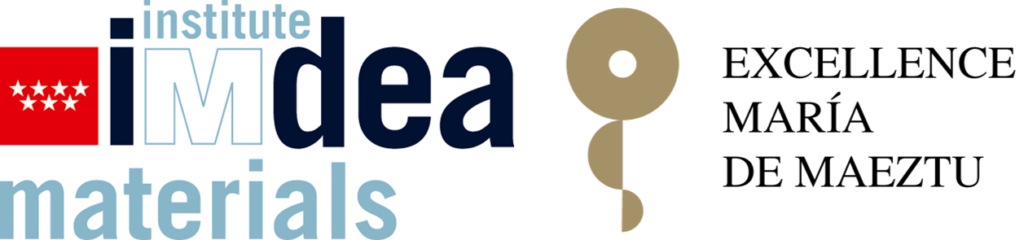
IMDEA Materials Institute (IMDEA) is a non-profit research institute (~120 researchers) devoted to carry out research in Materials Science and Engineering in Madrid (Spain). IMDEA is committed to the excellence in research and to foster technology transfer to the industrial sector. IMDEA holds a well-established international reputation in the areas of processing, microstructural analysis, characterization and multiscale modelling of advanced materials for applications in transport, energy and information technology as well as on the exploration of emerging materials and processes for sustainable development. Research activities and technology transfer to industry at IMDEA is carried out within the framework of research projects funded by national or international organizations or directly through contracts with industry. Currently, IMDEA participates in 50 EU research projects (11 as a coordinator) and has 70 direct R&D contracts with industrial companies.
The main research activities of IMDEA Materials Institute within frame of the DELIGHTED project focus on a thorough microstructural characterization of the developed steels using state of the art techniques, their tensile and fatigue properties, as well as properties of individual microstructural constituents.
Team members:
- Dr. Ilchat Sabirov, Technical coordinator, ilchat.sabirov@imdea.org
- Dr. Jon Molina-Aldareguia, Senior researcher, jon.molina@imdea.org
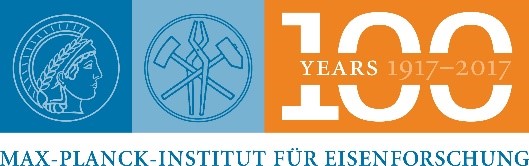
The international team of the Max-Planck-Institut für Eisenforschung (MPIE) conducts advanced basic materials research related to the fields of mobility, energy, infrastructure, medicine and digitalisation. We focus on nanostructured metallic materials as well as semiconductors and analyse down to their atomic and electronic scales. This enables us to develop new, tailor-made structural and functional materials embracing their synthesis and processing, characterization and properties, as well as their response in engineering components exposed to real operating environments.
The dynamic structure of the institute and the very intensive cooperation between the departments and researcher teams worldwide are ideally suited to provide answers to the currently emerging global issues of CO2-reduced and sustainable production and manufacturing, the complete conversion of energy supply and automotive drive technology, the synergies between machine learning and materials research and production, and the need for new high-performance materials for safety, weight-reduced transport and functional innovations based on excellent basic research.
The basic budget of the institute comes from the Max Planck Society (MPG) and partly from the Steel Institute VDEh. This public-private partnership is unique within the MPG and the European industry and enables up-to-date basic research with a high application relevance.
Team members:
- Dirk Ponge, Supervising scientist, d.ponge@mpie.de
- Katja Hübel, Research coordinator, k.huebel@mpie.de
- Mohamed Elkot (PhD), Scientist in charge, m.elkot@mpie.de
- Birgit Neumann, Administrative officer, b.neumann@mpie.de
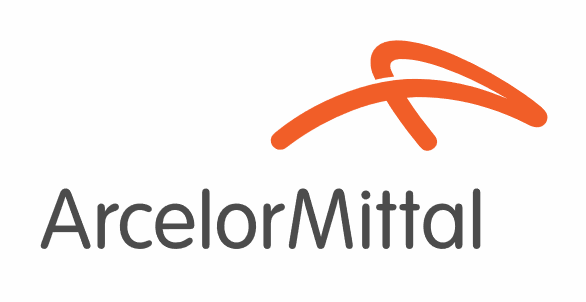
OCAS (OnderzoeksCentrum voor de Aanwending van Staal – Research Centre for the Application of Steel) is an advanced, market-oriented research centre providing steel and metal-based products, services and solutions to metal processing companies worldwide. OCAS is a daughter company of FINOCAS and ArcelorMittal Belgium, FINOCAS being a joint-venture between the Flemish Region and ArcelorMittal Belgium. Within ArcelorMittal, OCAS is known as ArcelorMittal Global R&D Gent and is as such in charge of all ArcelorMittal R&D projects within the market of general industry for flat carbon steel.
OCAS is equipped with state-of-the-art R&D tools and facilities in its laboratories in Zelzate and Gent-Zwijnaarde (Belgium). The research centre valorizes know-how by product and solution development. OCAS has a highly qualified team of over 140 researchers and engineers with an international orientation. The laboratories have a unique range of state-of-the-art analysis and simulation tools, and even a complete lab scale steel production line integrated in the Metal Processing Centre Gent (MPC), which is a third linked party of OCAS in the DELIGHTED project. MPC will provide the facilities for the casting, thermo-mechanical processing and ageing, as they the most suitable for the given type of processing. OCAS’ core expertise and competences include:
- Metallurgy: steel grade developments (e.g. high strength steels, electrical steel, etc.) and metal processing (casting, rolling, heat treatment);
- Surfaces: enhanced aesthetics of steel, corrosion protection, pre-treatments and surface preparation, multifunctional organic coatings (self-cleaning, bio-active, etc.), enamels, metallic coatings;
- Applications and solutions: structural component design, prototyping, welding, Finite Element Method (FEM) simulation and Computational Fluid Dynamical (CFD) modeling.
All activities are supported by a state-of-the-art material characterization and testing laboratory, with unique facilities in coating, metal characterization and processing tools.
Team members:
- Dr. Lode Duprez, Principal Investigator, lode.duprez@arcelormittal.com
- Dr. Aniruddha Dutta, Researcher, aniruddha.dutta@arcelormittal.com
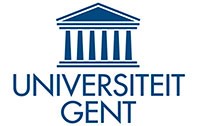
Universiteit Gent (UGENT) has more than 40,000 students. A significant part of the expertise of the Department of Electrical Energy, Metals, Mechanical constructions & Systems lays in the areas of Metals Science and Technology (MST) and Mechanics of Materials and Structures (MMS). The research is performed in close collaboration with the industrial and academic partners and addresses materials engineering problems of an applied nature, but rooted in the fundamental understanding of materials behavior. The activities of the MST-group are closely related to the presence of a vast amount of logistic and experimental facilities for manufacturing (including a HD simulator…), mechanical testing (including split Hopkinsion bar facilities) and thorough microstructural characterization (e.g. optical microscopy, X-ray diffraction, SEM, ESEM, FIB-SEM, HR-TEM). The entire chain of metallurgical research can be done in-house, which offers a truly unique environment for an academic research facility. One of the specialized research fields is the investigation and characterization of microstructures and textures by means of phase/orientation contrast microscopy (EBSD) which is extended also to transmission Kikuchi diffraction and 3D-EBSD in small (20x20x20µm) and large (up to few mm³) scales. This technology is of key importance in the DELIGHTED project as it allows characterizing the physical processes occurring during thermo-mechanical treatment of steels.
Team members:
- Prof. Roumen Petrov, Principal investigator, Roumen.Petrov@UGent.be
- Florian Vercruysse, Researcher, Florian.Vercruysse@UGent.be
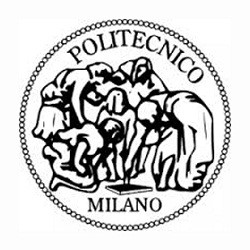
Politecnico di Milano (POLIMI) is the most important technical university in Italy and in the QS ranking is at 9th position in 2020 in Engineering – Mechanical, Aeronautical & Manufacturing. The institution of Politecnico di Milano involved in this research programme is Dipartimento di Meccanica, where the research group focused on steel making and metallurgical processes is operating. The skills of this group include: smelting and refining processes for the improvement of product quality and plant innovation; solidification (continuous casting, ingot casting, foundry, welding); plastic deformation of metal alloys and related mechanical and formability properties obtained from end products. The activities of the group are closely related to the presence of a wide amount of experimental facilities for mechanical testing (cyclic tests, fatigue tests, fracture characterization,) and thorough microstructural characterisation (e.g. SEM-EBSB, FEG-SEM, X-ray diffraction with also the Euler craddle). One of the specialised research fields is the investigation of the deformation of metal sheet by the use FLD determination.
POLIMI will design, coordinate and perform the production of the connections of a vineyard tractor cabin with a tractor frame using light-weight steel developed within frame of the DELIGHTED project. The components will be produced at SDF-Group production site in Treviglio (Italy). SDF-Group is subcontracted for the production of the dies, connections and experimental crash test simulating the overturning of the vine-yard tractor. A theoretical model will be developed to predict the local plastic deformation and validated using experimental results from crash test.
Team members:
- Prof. Carlo Mapelli, Principal investigator, carlo.mapelli@polimi.it
- Dr. Silvia Barella, Researcher, silvia.barella@polimi.it
- Mr. Davide Mombelli, Researcher, davide.mombelli@polimi.it
Funded by
The DELIGHTED project has received funding from the European Union’s Research Fund for Coal and Steel under grant agreement nº 899332.
Start of the project 01/07/2020 – End of the project 29/02/2024
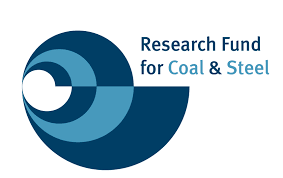
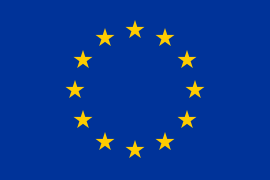
Contact us
IMDEA Materials Institute (project Coordinator)
Eric Kandel, 2 Tecnogetafe
28906, Getafe, Madrid (Spain)
Phone: (+34) 91 549 34 22
Fax: (+34) 91 550 30 47